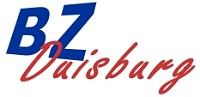
|
Redaktion Harald Jeschke
|
|
Weltpremiere in Duisburg: Erstmaligen Einsatz von
Wasserstoff im Hochofen
|
NRW-Wirtschaftsminister Pinkwart
startet bei thyssenkrupp Versuchsreihe zum erstmaligen
Einsatz von Wasserstoff im Hochofen
Duisburg, 11. November
2019 - thyssenkrupp Steel hat in Duisburg eine
Weltpremiere gefeiert: Der Duisburger Stahlhersteller
startete eine Versuchsreihe zum Einsatz von Wasserstoff
im laufenden Hochofenbetrieb. Es sind die bislang ersten
Tests dieser Art. Sie dienen dem Ziel, die bei der
Stahlherstellung entstehenden CO2-Emissionen
nachhaltig zu reduzieren. Der Versuchsstart im Beisein
von NRW-Wirtschafts- und Digitalminister Prof. Dr.
Andreas Pinkwart markiert einen Meilenstein in der
Transformation zur klimaneutralen Stahlproduktion.
Zwischenziel 2030: 30 Prozent
weniger Emissionen
Die nun gestartete Versuchsreihe
ist ein wichtiger Baustein der Klimastrategie von
thyssenkrupp. Bis 2050 will das Unternehmen klimaneutral
werden. Bereits bis zum Jahr 2030 sollen die Emissionen
aus Produktion und Prozessen (die sogenannten Scope
1-Emissionen) im eigenen Unternehmen sowie die Emissionen
aus dem Bezug von Energie (Scope 2) um 30 Prozent
reduziert werden. „Wir haben uns mit unserer
Klimastrategie ein klares Ziel gesetzt.“, sagte Dr. Klaus
Keysberg, Mitglied des Vorstands der thyssenkrupp AG,
zuständig für Materialgeschäfte des Konzerns.
„Die Stahlproduktion nimmt für die Erreichung unserer Klimaziele eine
wichtige Rolle ein, denn der Hebel der Sparte bei der
Senkung der Emissionen ist groß. Deswegen treiben wir den
Wandel zur Wasserstofftechnologie mit aller Kraft voran.“
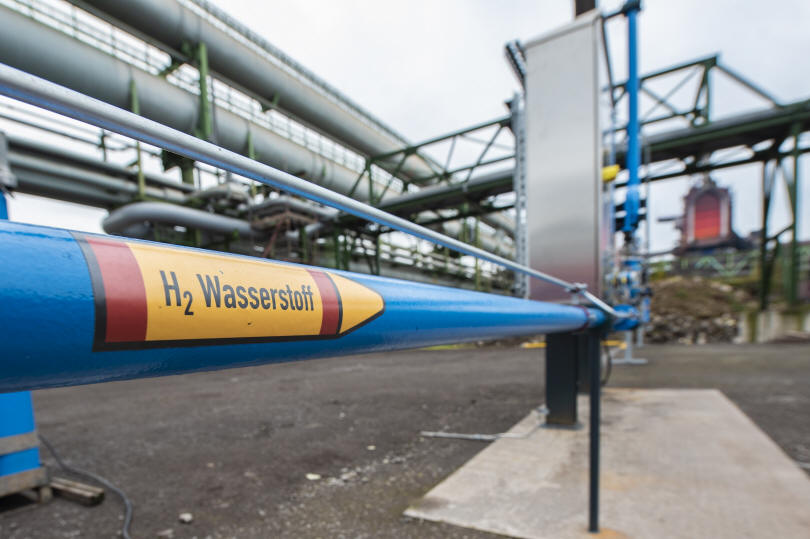
Transferstelle, an der der
Wasserstoff ins System eingespeist wird. Im Hintergrund:
Hochofen 8.
Wasserdampf statt CO2
Beim klassischen
Hochofenprozess werden für die Herstellung von einer
Tonne Roheisen rund 300 Kilogramm Koks und 200 Kilogramm
Kohlenstaub benötigt. Der Kohlenstaub wird im unteren
Schachtbereich des Hochofens als zusätzliches
Reduktionsmittel über 28 sogenannte Blasformen
eingeblasen. Zum Versuchsstart wurde heute an einer
dieser Blasformen am Hochofen 9 Wasserstoff injiziert.
Damit beginnt eine Versuchsreihe, in der thyssenkrupp
Steel den Einsatz von Wasserstoff schrittweise erst auf
alle 28 Blasformen dieses Hochofens und ab dem Jahr 2022
dann auf alle drei weiteren Hochöfen ausweiten will. Der
Vorteil: Während beim Einsatz von Einblaskohle CO2-Emissionen
entstehen, entsteht beim Einsatz von Wasserstoff
Wasserdampf. Somit können bereits an dieser Stelle im
Produktionsprozess bis zu 20 Prozent CO2eingespart
werden.
„Der heutige Tag ist wegweisend
für die Stahlindustrie“, sagte Premal Desai, Sprecher des
Vorstands von thyssenkrupp Steel Europe. „Wir leisten
hier Pionierarbeit. Die Nutzung von Wasserstoff ist der
entscheidende Hebel für eine klimaneutrale
Stahlproduktion. Der heutige Versuch ist ein weiterer
wichtiger Schritt in der Transformation unserer
Produktion, an deren Ende grüner Stahl stehen wird.
Gleichzeitig sehen wir, was alles möglich ist, wenn
Unternehmen und Politik gemeinsam auf ein Ziel
hinarbeiten. Für die Förderung des Projekts sind wir dem
Land NRW sehr dankbar.“
Förderung durch Land NRW
Das Projekt wird im Rahmen der
von der Landesregierung gestarteten Initiative
IN4climate.NRW gefördert und vom
Betriebsforschungsinstitut des VdEH (BFI)
wissenschaftlich begleitet. Im April 2019 übergab die
Landesregierung den Förderbescheid für die erste
Testphase. NRW-Wirtschafts- und Digitalminister Prof. Dr.
Andreas Pinkwart: „Das Projekt ist ein wichtiger Schritt
auf dem Weg zu einer treibhausgasneutralen Industrie und
ein schönes Beispiel dafür, wie innovative
Schlüsseltechnologien aus Nordrhein-Westfalen heraus
entwickelt werden können. Wir müssen die Nutzung von
Wasserstoff im Industriesektor weiter vorantreiben, denn
sie bietet gerade bei der Stahlherstellung große
Chancen“.
Vom Labor in den
Industriemaßstab
Der Versuchsstart markiert auch
den Übergang des Projekts in den industriellen Maßstab.
In den letzten Monaten wurden vorgelagerte Untersuchungen
und Simulationsrechnungen durchgeführt. Mit dem Versuch
im laufenden Hochofen wird das Projekt auf die nächste
Ebene gehoben. „Wir wollen durch die Nutzung von
Wasserstoff die Emissionen senken und gleichzeitig
weiterhin Roheisen in gewohnter Qualität produzieren“,
erläutert Dr. Arnd Köfler, Produktionsvorstand von
thyssenkrupp Steel Europe. „Gleichzeitig gilt auch: wir
betreten mit der Versuchsreihe am Hochofen 9
technologisches Neuland. Es geht jetzt darum, den
Betriebsablauf im Hochofen kontinuierlich zu analysieren
und auszuwerten. Die Ergebnisse werden uns helfen, die
Ausweitung des Wasserstoffeinsatzes auf alle 28
Blasformen des Hochofens gezielt anzugehen.“
Wasserstoff-Infrastruktur
gewinnt an Bedeutung
Wasserstoff wird in den kommenden Jahrzehnten ein
zentraler Treiber für die Klimastrategie von thyssenkrupp
Steel sein. Nach der Umstellung der Hochöfen plant das
Unternehmen ab Mitte der 2020er-Jahre den Aufbau von
großtechnischen Direktreduktionsanlagen, die dann mit
wasserstoffhaltigen Gasen betrieben werden. Der dort
produzierte Eisenschwamm wird zunächst in den bestehenden
Hochöfen eingeschmolzen, soll langfristig aber in
Elektrolichtbogenöfen mit Hilfe erneuerbarer Energien zu
Rohstahl verarbeitet werden.
Mit Air Liquide ist beim
Einblasversuch ein Projektpartner an Bord, der über
Expertise in der gesamten Wasserstoff-Wertschöpfungskette
von der Produktion über die Speicherung bis hin zur
Entwicklung von Endverbraucheranwendungen verfügt. Gilles
Le Van, Vorsitzender der Geschäftsführung von Air Liquide
Deutschland: „Wasserstoff ist der Schlüssel zu
Energiewende und industrieller Transformation
gleichermaßen. Dieses besondere Molekül kann beides sein:
Grundstoff für die Wirtschaft und Medium zur
Energiespeicherung und
-rückgewinnung. Bei Air Liquide sind wir vom Potenzial
einer weltweiten Wasserstoffwirtschaft überzeugt – und
bringen mehr als 60 Jahre Erfahrung und Innovationskraft
in diesem Feld in die gemeinsame Projektarbeit ein. So
gestalten wir zusammen die Wasserstoffzukunft in
Deutschland und tragen zum Erreichen der Klimaziele bei.“
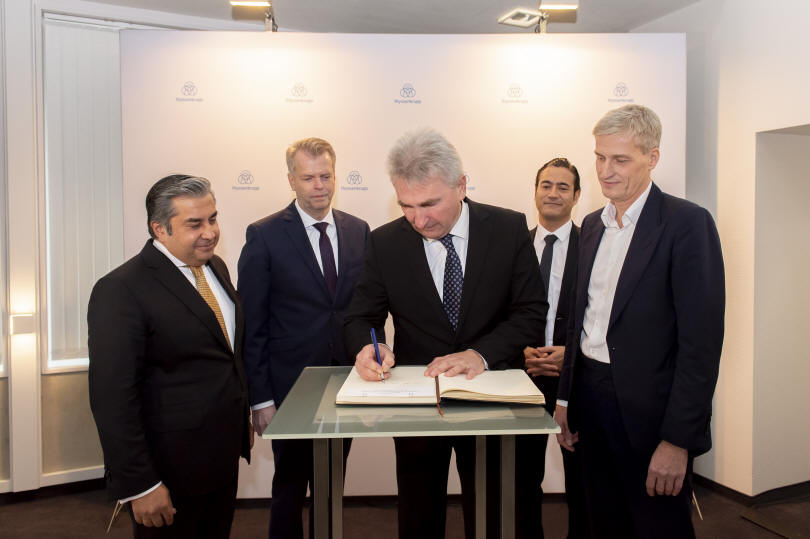
NRW-Wirtschafts- und
Digitalminister Prof. Dr. Andreas Pinkwart beim Eintragen
ins Goldene Buch – gemeinsam mit (v.l.n.r.) Premal Desai,
Sprecher des Vorstands thyssenkrupp Steel Europe,
thyssenkrupp AG Vorstand Dr. Klaus Keysberg, Gilles Le
Van, Vorsitzender der Geschäftsführung von Air Liquide
Deutschland, und thyssenkrupp Steel Europe
Produktionsvorstand Dr. Arnd Köfler.
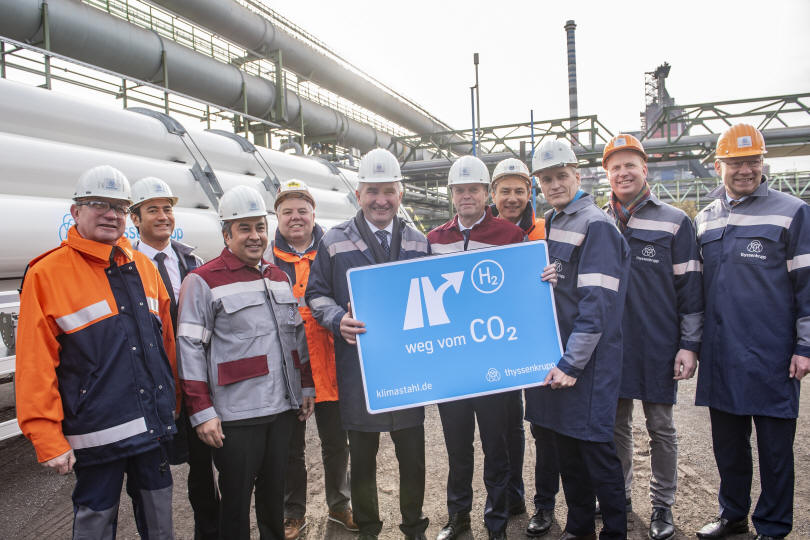
Einblasversuch Hochofen - v.l.: Dr. Jens Reichel, Leiter
Technische Dienstleistungen & Energie thyssenkrupp Steel
Europe, Gilles Le Van, Vorsitzender der Geschäftsführung
von Air Liquide Deutschland, Premal Desai, Sprecher des
Vorstands thyssenkrupp Steel Europe, der stellvertretende
thyssenkrupp Steel Europe Betriebsratsvorsitzende Horst
Gawlik, NRW-Wirtschafts- und Digitalminister Prof. Dr.
Andreas Pinkwart, thyssenkrupp AG Vorstand Dr. Klaus
Keysberg, der thyssenkrupp Steel Europe
Gesamtbetriebsratsvorsitzende Tekin Nasikkol,
thyssenkrupp Steel Europe Produktionsvorstand Dr. Arnd
Köfler, Henning Rehbaum, Sprecher für Wirtschaft, Energie
und Landesplanung der CDU-Fraktion im Landtag NRW, und
Stefan Schreiber, Hauptgeschäftsführer IHK zu Dortmund.
|
Ein halbes Jahrhundert bei
thyssenkrupp Steel
|
Rund 30 Mitarbeiter und Mitarbeiterinnen feiern goldenes
Dienstjubiläum Duisburg, 8. November 2019 - Ein seltenes Arbeitsjubiläum gab
es dieser Tage bei thyssenkrupp Steel zu feiern: 50 Jahre
arbeiten die 31 Jubilare nun im Konzern. Das ist ein halbes
Jahrhundert voller Veränderungen. 1992 fusioniert die
Friedrich Krupp AG mit der Hoesch AG, 1997 schließen sich
die Stahlbereiche von Thyssen mit Krupp zusammen, zwei Jahre
später nimmt die ThyssenKrupp AG ihre Arbeit auf.
In
den 2000ern gehen ein neuer Hochofen und die modernste
Tuchfilteranlage weltweit in Betrieb, 2019 startet
thyssenkrupp Steel ein wegweisendes Projekt für eine
klimafreundliche Stahlproduktion: Wasserstoff statt Kohle.
All diese und noch viele weitere Veränderungen haben die 31
Jubilare miterlebt und mitgestaltet. „Für mich fühlt es sich
auch nach all den Jahren noch gut an, bei thyssenkrupp Steel
zu arbeiten. Ich bin immer gerne zur Arbeit gegangen und tue
das auch heute noch“, sagt Jubilar Erwin Göpner. Er
kümmert sich um die Instandsetzung von Maschinen in einer
Spezialwerkstatt in Ruhrort. Auch Jubilarin Jutta Maciej,
tätig im Personalcenter, Funktionsbereich HRD, fühlt sich
nach wie vor wohl bei thyssenkrupp Steel. „Natürlich gab es
zwischendurch Höhen und Tiefen im Konzern. Aber ich schaue
lieber nach vorne als zurück“, sagt sie. Zeitreise in
die Vergangenheit und Blick in die Zukunft „Langjährige
Mitarbeiterinnen und Mitarbeiter leisten durch ihre
Erfahrung einen wertvollen Beitrag zum Unternehmenserfolg“,
betont Sabine Maaßen, Arbeitsdirektorin der thyssenkrupp
Steel Europe AG. Im Rahmen einer feierlichen Veranstaltung
bedankte sich Arnd Köfler, Produktionsvorstand bei
thyssenkrupp Steel, für fünf Jahrzehnte Engagement und
Loyalität der Jubilare: „Ein goldenes Dienstjubiläum ist in
der heutigen schnelllebigen Zeit etwas ganz Besonderes.“
Auf dem Programm stand unter anderem eine Zeitreise
durch die letzten 50 Jahre Unternehmensgeschichte: Wie haben
sich die Sicherheitshelme, wie die Büroarbeit verändert? Mit
einem Auge blickten die Jubilare aber auch gemeinsam mit dem
Vorstand in die Zukunft. Zum Abschluss der Feier bekamen die
Jubilare zum Dank ein kleines Präsent mit persönlicher
Widmung des Vorstandes überreicht – ein hochwertiges Bild
eines Hochofens, damit sie diesen Teil ihres Lebens auch in
der nahenden Rente nicht vergessen.

Goldenes Dienstjubiläum feiert nicht jeder: thyssenkrupp
Steel bedankte sich kürzlich im Rahmen einer feierlichen
Veranstaltung bei 31 Mitarbeiterinnen und Mitarbeiter für
ihr langjähriges Engagement und ihre Loyalität. Eine
Zeitreise durch die letzten 50 Jahre und ein Zauberer waren
zwei der Highlights im Programm.

Erwin Göpner feierte sein Dienstjubiläum bei thyssenkrupp
Steel mit seiner Frau Marlies. Ob der Zusammenschluss von
Thyssen und Krupp, die modernste Tuchfilteranlage weltweit
oder das aktuelle Projekt für eine klimafreundliche
Stahlproduktion bei thyssenkrupp Steel – Erwin Göpner hat so
einige Veränderungen im Konzern miterlebt und mitgestaltet.
Fotos: thyssenkrupp Steel
|
Investition in Hightech und
Zukunft: thyssenkrupp Steel legt Grundstein für neue
Feuerbeschichtungsanlage in Dortmund
|
Duisburg,
30. Oktober 2019 - Die neue und hochmoderne
Feuerverzinkungsanlage FBA10 von thyssenkrupp Steel am
Standort Dortmund nimmt Form an. Nach Erteilung der
Genehmigung durch die zuständige Bezirksregierung in
Arnsberg erfolgte heute die symbolische Grundsteinlegung.
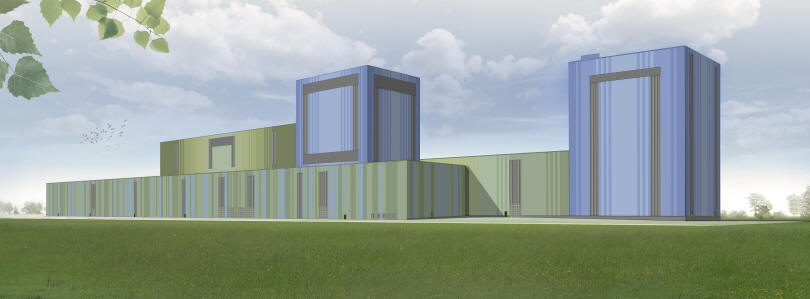
nsicht der geplanten Feuerbeschichtungsanlage in
Dortmund.
Gemeinsam mit Ministerpräsident Armin Laschet ebnete
thyssenkrupp Steel damit den Weg für die zehnte Anlage
dieser Art im Ruhrgebiet, die 2021 in Betrieb genommen
werden soll. Premiumoberflächen und dauerhafter Schutz
vor Korrosion im Automobilbau Feuerverzinkte Produkte
gewinnen in der Automobilindustrie zunehmend an
Bedeutung.
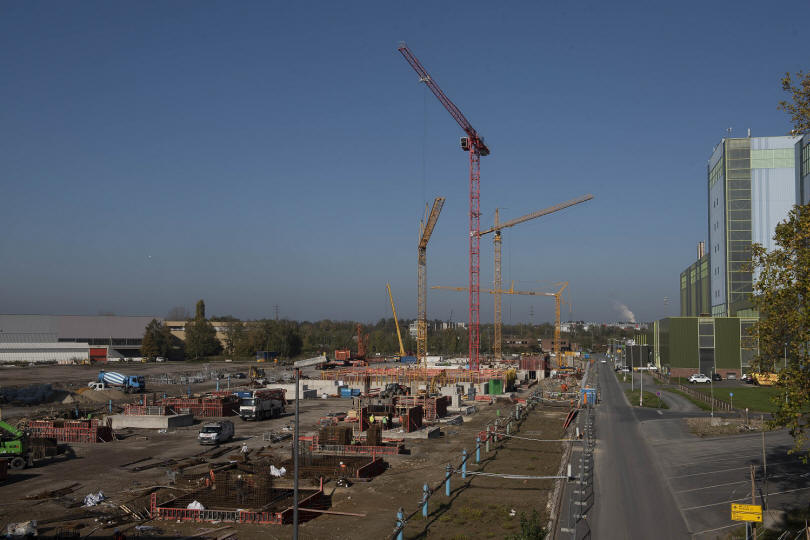
Die Baustelle der FBA 10 auf der Westfalenhütte in
Dortmund.
Die Oberflächenbehandlung des Stahls mit Zink sorgt für
hohen Korrosionsschutz und damit für die Langlebigkeit
der verbauten Teile im Fahrzeug. „In der
Automobilindustrie findet ein substantieller Wechsel von
elektrolytisch verzinkten zu feuerverzinkten Stählen
statt“, sagte Premal Desai, Sprecher des Vorstands von
thyssenkrupp Steel.
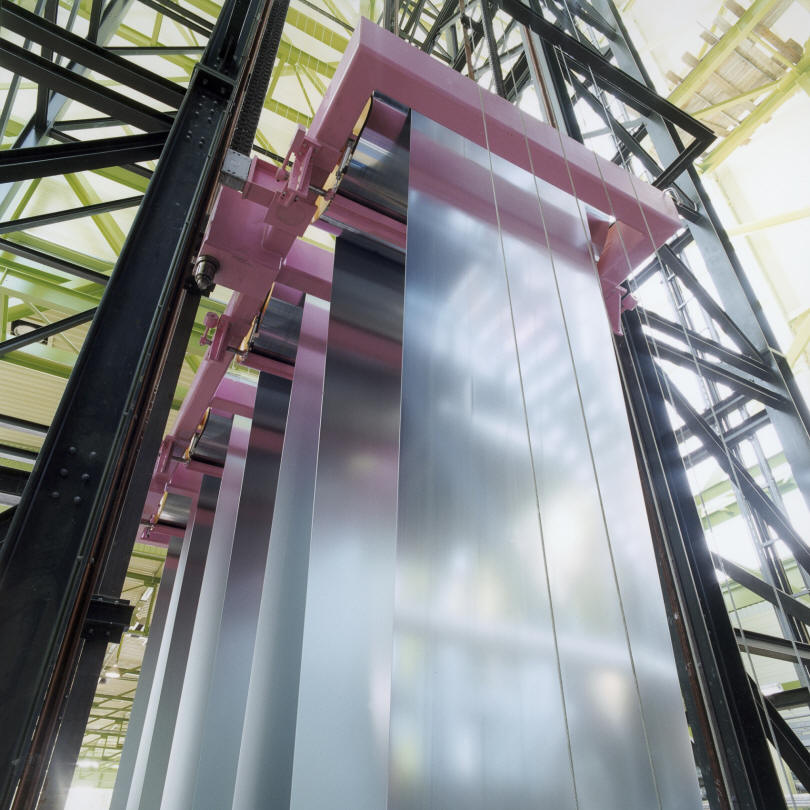
ZM Ecoprotect® – Zink-Magnesium-Überzug in
Außenhautqualität für hochwirksamen Korrosionsschutz und
leichte Verarbeitung.
„Mit der
neuen Feuerbeschichtungsanlage begleiten wir diesen Trend
und nutzen das entsprechende Marktpotenzial. Die Anlage
ist ein zentraler Baustein für unseren Ansatz, uns durch
HightechProdukte im Wettbewerb zu differenzieren. Die
FBA10 ist damit ein wichtiger Schritt für eine
erfolgreiche und nachhaltige Entwicklung von thyssenkrupp
Steel.“
Die FBA10 wird Stähle für Innenteile und
Außenhautwendungen von Fahrzeugen fertigen und auch die
hochinnovativen Zink-Magnesium-Produkte anbieten, die
durch eine geringe Auflagenstärke material-,
kostensparend und nachhaltig zugleich sind. Dortmund im
Zentrum für feuerverzinkte Produkte Wenige Meter neben
der neuen FBA10 betreibt thyssenkrupp seit 2001 bereits
eine Feuerbeschichtungsanlage, die FBA8. Zukünftig werden
hier zusammen eine Millionen Tonnen feuerverzinkte
Produkte von den Bändern der beiden hochmodernen Anlagen
rollen. Der Standort Dortmund und die Region Ruhrgebiet
gewinnen damit weiter an Bedeutung als Kompetenzzentrum
für diese Technologie.
Ministerpräsident Armin Laschet: „Die neue
Feuerverzinkungsanlage ist das beste Beispiel dafür, dass
Stahl für Innovation und moderne Technologien steht. Der
heutige Tag zeigt deutlich: Stahl und thyssenkrupp haben
eine Perspektive hier im Ruhrgebiet! Ein starker
Standort, der sich dem Wandel immer gestellt hat und
heute auch stellt. Diesen Wandel gestaltet die
Landesregierung mit der Ruhr-Konferenz mit und sorgt
dafür, dass sich diese Region zu einer wirtschaftlich
starken Zukunftsregion weiterentwickelt“
Ministerpräsident Armin Laschet weiter:
„Nordrhein-Westfalen will als Industrieland
Innovationstreiber, etwa auf dem Feld der klimaneutralen
Herstellung von Stahl sein. Wir wollen zeigen, dass
erfolgreicher Klimaschutz und ein starker
Wirtschaftsstandort verbunden werden können und dass wir
überzeugende und nachhaltige Antworten auf die
Herausforderungen der Energiewende und des Klimawandels
geben können.“
Ullrich Sierau, Oberbürgermeister der Stadt Dortmund:
„Obwohl das Westfalenhüttengelände zu einem Jobmotor für
die Logistik geworden ist, hat die Stahlveredelung hier
ihre Heimat. Dafür haben wir immer Flächen vorgehalten.
Ich bin sehr froh, dass jetzt diese Investition den
Stahlstandort Westfalenhütte zukunftsträchtig macht.
Der Bau der neuen Feuerbeschichtungsanlage knüpft
zukunftsweisend an beste Stahl-Traditionen an und macht
die Westfalenhütte auch zu einem bedeutenden
Kompetenzzentrum für feuerverzinkte Produkte.
Diese hochwertigen Beschichtungen sowie über 100
hochqualifizierte Arbeitsplätze passen zu Dortmunds
Charakter einer technologieorientierten Metropole, die
den Strukturwandel erfolgreich angegangen ist.“
Hans-Josef Vogel, Regierungspräsident des
Regierungsbezirkes Arnsberg: „Hier zeigt sich deutlich:
Strukturwandel gelingt mit dem Blick auf zukunftsfähige
Technologien, allerdings nicht ohne die jahrzehntelange
Expertise des Stahlstandortes Dortmund. Es braucht gerade
im Strukturwandel das Vertrauen von Unternehmen in die
Region – und genau das beweist thyssenkrupp Steel mit
dieser Investition. Die weiterverarbeitenden
Industriebetriebe im südwestfälischen Raum profitieren
davon.“ Er dankte für die gute Zusammenarbeit. Die
Genehmigungsverfahren konnten somit zügig durchgeführt
werden.
Investition schafft Arbeitsplätze
Mit der Investition im niedrigen dreistelligen
Millionenbereich stärkt thyssenkrupp Steel den Standort
Dortmund, an dem derzeit rund 1.300 Mitarbeiterinnen und
Mitarbeiter tätig sind. Durch die FBA10 werden über 100
weitere Arbeitsplätze hinzukommen.
„Die FBA10 ist eine Investition in den Standort und ein
wichtiges Signal an die Belegschaft: thyssenkrupp Steel
investiert in die Zukunft und in neue, hoch qualifizierte
Arbeitsplätze. Eine Anlage wie die FBA10 wird für
Jahrzehnte gebaut und ist genau das richtige Zeichen in
unruhigen Zeiten“, betonte Tekin Nasikkol,
Gesamtbetriebsratsvorsitzender von thyssenkrupp Steel.
Daten und Fakten:
Die fertige Anlage wird eine Länge von rund 350 Metern
besitzen und an der höchsten Stelle etwa 65 Meter messen.
Verbaut werden unter anderem 8.000 Tonnen Stahl und
24.000 Kubikmeter Beton. Darunter sind auch 180
Bohrpfähle, die mit einem Durchmesser von etwa 1,5 Metern
bis zu elf Meter tief in den Boden reichen. Pro Jahr wird
die Anlage rund 600.000 Tonnen feuerverzinkten Stahl
herstellen. Die Investitionen belaufen sich auf einen
niedrigen dreistelligen Millionenbetrag.
|
thyssenkrupp Steel: Dritte
Tuchfilteranlage in Duisburg nimmt Form an
|
Duisburg, 11. Oktober 2019 - Hitzerekorde, Greta-Effekt,
CO2-Steuer – der Klimawandel beherrscht die Schlagzeilen
und stellt andere Umweltthemen in den Schatten. Neben CO2
sind aber auch andere Stoffe ein wichtiges Thema beim
Umweltschutz. Dazu gehört etwa Feinstaub, der unter
anderem an Sinteranlagen in der Stahlproduktion entsteht.
Deswegen hat thyssenkrupp Steel am Standort Duisburg
insgesamt rund 100 Millionen Euro in ein
Tuchfilterprojekt investiert, um die Abluft der
Sinteranlage zu reinigen. Schon im Frühjahr 2020 soll
dann auch die letzte von drei Tuchfilteranlagen in den
Betrieb gehen. Beim Bau dieser Anlage wurde nun ein
weiterer Teil des Filters in Position gebracht: mit einem
Gewicht von 17 Tonnen keine leichte Aufgabe, für die zwei
große 80- und 220-Tonnen Krane bereitstanden.
Weltweit größte und effektivste Anlage Beim „Sintern“
werden Eisenerze mit Koks und anderen Stoffen wie Kalk
vermischt, auf rund 1.200 Grad erhitzt und
zusammengebacken. Um den Koks zu verbrennen, wird mit
großen Gebläsen Luft durch die Mischung gesaugt. Dabei
ist Staubbildung unvermeidlich. Den größten Teil dieses
Staubs fangen üblicherweise Elektrofilter ein – mit den
großen Tuchfilteranlagen setzt thyssenkrupp allerdings
neue Maßstäbe bei der Luftreinigung und fängt auch
kleinste Staubpartikel ein.
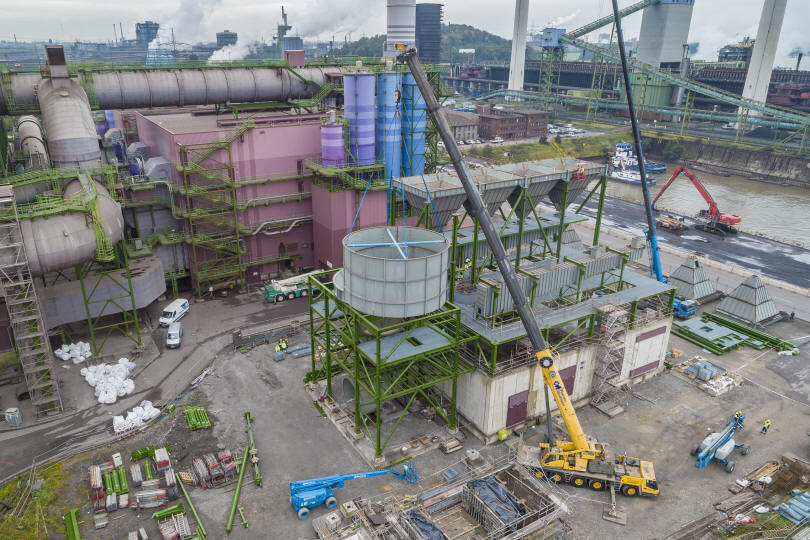
Ein Kran bringt das 17 Tonnen schwere Teil des Filters in
Position.
Die Sinteranlage im Duisburger Norden besteht aus drei
Bändern. Ein Tuchfilter für das kleinste Band ist bereits
seit 2011 in Betrieb, 2017 wurde die Filteranlage am
größten der drei Bänder in Betrieb genommen. Jetzt folgt
Band Nummer drei. „Die Tuchfilteranlage am Standort
Duisburg ist eine der weltweit größten und effektivsten
Anlagen dieser Art“, sagte Projektleiter Tibor Hänsel.
„In wenigen Monaten endet dann sehr erfolgreich eines
unserer größten Projekte für saubere Luft.“
Behördliche Auflagen werden übererfüllt „Die
Investitionen zahlen sich aus, denn die Tuchfilteranlagen
bedeuten insgesamt einen großen Schritt bei der
Verbesserung der Luftqualität“, sagte Andreas Theuer,
Leiter des Bereichs Umwelt- und Klimaschutz bei
thyssenkrupp Steel. Die Grenzwerte für Feinstaub werden
damit übererfüllt. „Wir reinigen die Luft zu 99,9 Prozent
von Feinstaub“, so Theuer. Diese deutliche Verbesserung
der Luftqualität in der unmittelbaren Nachbarschaft ist
zugleich ein wichtiger Beitrag für die Umwelt im
Ruhrgebiet und ein klares Bekenntnis zum Standort
Duisburg.
|
Thyssenkrupp untersucht
Optionen für Produktion und Einsatz von klimafreundlichem
Wasserstoff
|
Duisburg, 8. Oktober
2019 - Thyssenkrupp will die Produktion von klimafreundlichem
Wasserstoff fördern. Gemeinsam mit dem norwegische
Energieunternehmen Equinor und
Erdgasfernleitungsnetzbetreiber Open Grid Europe startet
der Stahlkonzern jetzt eine Machbarkeitsstudie, die die
Herstellung des Stoffs auf der Basis von Erdgas und
seinen Einsatz in der Versorgung des größten deutschen
Stahlwerks in Duisburg prüfen soll.
In der Studie werden mehrere Optionen für die Gewinnung
und den Transport von Wasserstoff zum
Thyssenkrupp-Standort sowie für den Transport und die
Speicherung von Kohlendioxid untersucht. Langfristiges
Ziel sei es, die Nutzung von Wasserstoff aus erneuerbaren
Energien zu erhöhen. Bis 2050 will Thyssenkrupp ein
klimaneutrales Unternehmen werden. Infos unter
www.thyssenkrupp-steel.com idr
|
50 Jahre
Oxygenstahlwerk von thyssenkrupp in Duisburg
|
Duisburg, 27. September
2019 - Innovationskraft, unternehmerischer Weitblick und
zukunftsweisende Technologie: am 29. September 1969 nahm
das Oxygenstahlwerk Duisburg-Bruckhausen seinen Betrieb
auf und markierte als eines der größten und modernsten
Stahlwerke der Welt einen Meilenstein der modernen
Stahlproduktion. Dort, wo Firmengründer August Thyssen
1891 das erste Siemens-Martin-Stahlwerk und wenig später
das erste Thomas-Stahlwerk errichten ließ, läuft es bis
heute. Seit dem ersten Befüllen des Konverters verließen
fast 190 Millionen Tonnen Stahl das Werk. Eine Menge, die
für rund 21.000 Eiffeltürme reichen würde.
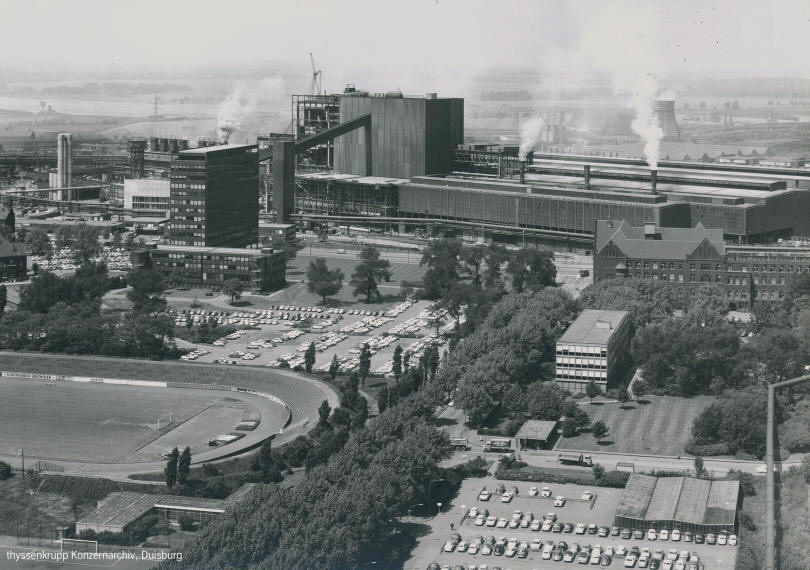
Historische Aufnahme des Oxygenstahlwerks
Duisburg-Bruckhausen aus dem Jahr der Inbetriebnahme,
1969.
Garant für Qualität, Volumen und
Wirtschaftlichkeit
Hochwertige Stähle in großen Mengen wirtschaftlich
produzieren – diesen Anspruch setzte das Oxygenstahlwerk
Bruckhausen in die Tat um: Dank innovativer Technologie
ließ sich mit zwei Sauerstoffaufblas-Konvertern Stahl von
hervorragender Qualität bei gleichzeitig hoher
Produktivität und Wirtschaftlichkeit erzeugen. „Mit
dieser Investition haben unsere Vorgänger Weitblick
gezeigt und schon vor 50 Jahren in den Stahl von heute
investiert“, sagt Thorsten Brand, Leiter des Bereichs
Rohstahl bei thyssenkrupp Steel. „Das Stahlwerk
Bruckhausen galt von Anfang an als eines der modernsten
der Welt. Es stand damals und steht heute für
fortwährende Anpassung an verbesserte Stahlqualität und
wechselnde Anforderungen unserer Kunden.“ Bruckhausen
brach Rekorde: Die Oxygen-Konverter produzierten im
40-Minutentakt rund 380 Tonnen Rohstahl – die höchsten
Werte, die bis dahin je erzielt werden konnten.
Kontinuierliche Modernisierung
steigert Sicherheit und Energieeffizienz
Damit es auch nach 1969 zu den
modernsten seiner Art zählte, wurde das Stahlwerk
Bruckhausen regelmäßig mit gezielten Investitionen auf
den neusten Stand der Technik gebracht. 1979 wurde es um
eine Stranggießanlage erweitert, die 1996 modernisiert
wurde. 1999 gingen die Gießwalzanlage, der Pfannenofen
und die
neue
Roheisen-Entschwefelung in Betrieb – Investitionen von
umgerechnet ca. 450 Millionen Euro. Das Herz der
Stahlherstellung, die beiden seit 1969 eingesetzten
Konverter, wurde 2013 und 2014 erneuert. „Das hat den
Blasprozess noch stabiler gemacht“, erklärt Thorsten
Brand.
Leiter des Bereichs Rohstahl bei thyssenkrupp Steel,
im Oxygenstahlwerk Duisburg-Bruckhausen vor einem der
Konverter.
„Durch engste Analysespannen steigern wir die Qualität
unserer Produkte immer weiter, wovon letztlich unsere
Kunden profitieren.“
Unternehmerischer Weitblick
Ausgeprägt war und ist beim
Duisburger Stahlhersteller auch das Gespür für globale
Megatrends. So erkannte man frühzeitig das Potenzial von
Digitalisierung und Automatisierung. Bereits seit Mitte
der 1980er Jahre werden die Prozesse mit
Computertechnologie gesteuert. Die Produktqualität machte
so einen entscheidenden Sprung nach vorn. Auch das Thema
Nachhaltigkeit stand früh im Fokus. Bereits bei der
Inbetriebnahme setzte man auf eine damals neue Technik
zur Staubvermeidung. Zudem wurden die im
Produktionsprozess anfallenden Schlacken früh als
Düngemittel in der Landwirtschaft oder als Füllstoffe für
den Straßenbau genutzt. Die Prozessgase aus den
Konvertern werden sinnvoll weiterverwendet: ein Teil
dient der Dampferzeugung, ein anderer Teil gelangt zur
Stromerzeugung in die unternehmenseigenen Kraftwerke.
Schmelzer in Bruckhausen: vom
Schwerstarbeiter zum Prozessmanager
Digitalisierung und
Automatisierung verbesserten nicht zuletzt auch die
Arbeitsbedingungen im Werk. Bis in die 1980er Jahre
hinein leisteten die Schmelzer dort körperliche
Schwerstarbeit bei großer Hitze und Staubbelastung. Mit
der Automatisierung verlagerten sich die Aufgaben hin zur
EDV-gestützten Steuerung und Kontrolle der
Produktionsprozesse. Das machte die Arbeit deutlich
sicherer, verlangte von den Mitarbeitern aber auch ganz
neue Fachkenntnisse und die Bereitschaft, mehr
Verantwortung zu übernehmen. Kurz: Das Berufsbild des
Schmelzers veränderte sich rasant. Entsprechend
anspruchsvoll gestaltet sich die heutige Ausbildung, die
so gut wie nichts mehr mit der Schmelzerlehre vor 50
Jahren gemeinsam hat.
Wandlungsfähiges Stahlwerk:
immer die passenden Produkte
Entscheidend für die
erfolgreiche Entwicklung des Standortes war auch die
kompromisslose Anpassung der Produktion an sich wandelnde
Markt- und Kundenbedingungen. Produktinnovationen und
neue Technologien prägten die Abnehmerbranchen,
entsprechend veränderten sich die Anforderungen der
Kunden an den Stahl: Neue Produkte und
Produktionsprozesse erforderten – und ermöglichten –
differenziertere Stahlgüten in zuverlässiger,
gleichbleibender Qualität. So wurde die Produktion in
Bruckhausen immer weiter ausdifferenziert und
maßgeschneiderte Produkte entwickelt. Heute produziert
das Oxygenstahlwerk rund 400 verschiedene Stahlgüten. Den
Schwerpunkt bilden Weißbleche für die Lebensmittel- und
Getränkeindustrie (etwa für Getränkedosen und
Lebensmittelkonserven) sowie Hightech-Stähle für die
Automobilindustrie, die als Strukturbauteile das Leben
der Insassen schützen oder für hochwertige Oberflächen
sorgen. Auch das Vormaterial für Elektroband, einen
Basiswerkstoff für E-Mobilität und erneuerbare Energien,
wird dort erzeugt. Damit ist das Stahlwerk Bruckhausen
auch 50 Jahre nach seiner Inbetriebnahme mit seinen 475
Mitarbeitern zentraler Bestandteil der Stahlproduktion
bei thyssenkrupp.
Daten und Fakten
Inbetriebnahme:
29.09.1969
Bauzeit: 18 Monate
Mitarbeiter*: 475
Kapazität*: 5,2
Mio. Tonnen/Jahr
Mittlere Chargengröße*:
375 Tonnen
Ausstattung*:
2 Konverter, 2 Argonspülanlagen zur
sekundärmetallurgischen Behandlung, 1 RH-Vakuumanlage, 1
Pfannenofen, 1 CAS-OB (LTS-Anlage), 1 Stranggießanlage, 1
Gießwalzanlage (GWA)
* Stand: September 2019
Gut zu wissen: So wird Roheisen
zu Stahl
Das Roheisen für das
Oxygenstahlwerk Duisburg-Bruckhausen liefern die Hochöfen
in Hamborn und Schwelgern. Das dort abgestochene Roheisen
wird mit sogenannten Chargierpfannen an die Konverter im
Oxygenstahlwerk gebracht. Roheisen enthält noch
unerwünschte Begleitelemente wie Silizium, Schwefel und
Phosphor. Der Schwefel wird dem Roheisen in einem
vorgeschalteten Prozess entzogen. Im Konverter werden
dann durch Aufblasen von Sauerstoff über eine
wassergekühlte Lanze die anderen unerwünschten
Begleitstoffe entfernt. Stahlschrott zur Kühlung und
Roheisen werden so bei Temperaturen von mehr als 2.500
Grad Celsius „gefrischt“. Innerhalb von rund 20 Minuten
entsteht aus Eisen Stahl, der schließlich immer noch
1.650 bis 1.720 Grad heiß ist. Dieser Rohstahl wird
entweder auf einer Stranggießanlage zu Stahlplatten
(„Brammen“) oder auf einer Gießwalzanlage zu sogenanntem
Warmband weiterverarbeitet, das später beispielsweise in
der Automobilindustrie eingesetzt wird.
|
|
Klimastrategie von thyssenkrupp:
Parlamentarischer Staatssekretär Oliver Wittke informiert
sich bei thyssenkrupp
|
Duisburg, 4. September 2019 -
Oliver Wittke, Staatssekretär des
Bundeswirtschaftsministeriums, besuchte während seiner
CO2-Tour das Duisburger Werk des Stahlherstellers von
thyssenkrupp. Er informierte sich ausführlich über die
Strategien des Ruhrkonzerns, wie dieser in Zukunft
CO2-Emissionen vermeidet und in andere Produkten
umwandelt.
Erster Halt am Hochofen
Am Hochofen wird es sich ganz deutlich zeigen: Die
Roheisenschmelze mittels Wasserstoff erfordert immense
Investitionen und einen kompletten Umbau der
Produktionskette. Noch in diesem Jahr beginnt der
Duisburger Stahlhersteller damit, statt Kohlenstoff
Wasserstoff in den Hochofen einzublasen und damit
chemisch das Eisen aus dem Erz zu lösen. Dabei entsteht
als Emission statt wie bisher Kohlendioxid (CO2) Wasser
bzw. Wasserdampf.
CO2 nutzen statt zu emittieren
Neben dem o.g. Verfahren der CO2-Vermeidung arbeitet
thyssenkrupp an einer Technologie, CO2 aus dem Hochofen
als Rohstoff für die Chemieproduktion, um neue Produkte
damit herzustellen – Carbon2Chem. Mit diesem Verfahren
kann der Konzern seine CO2-Emissionen insbesondere in der
Stahlerzeugung in Zukunft reduzieren.
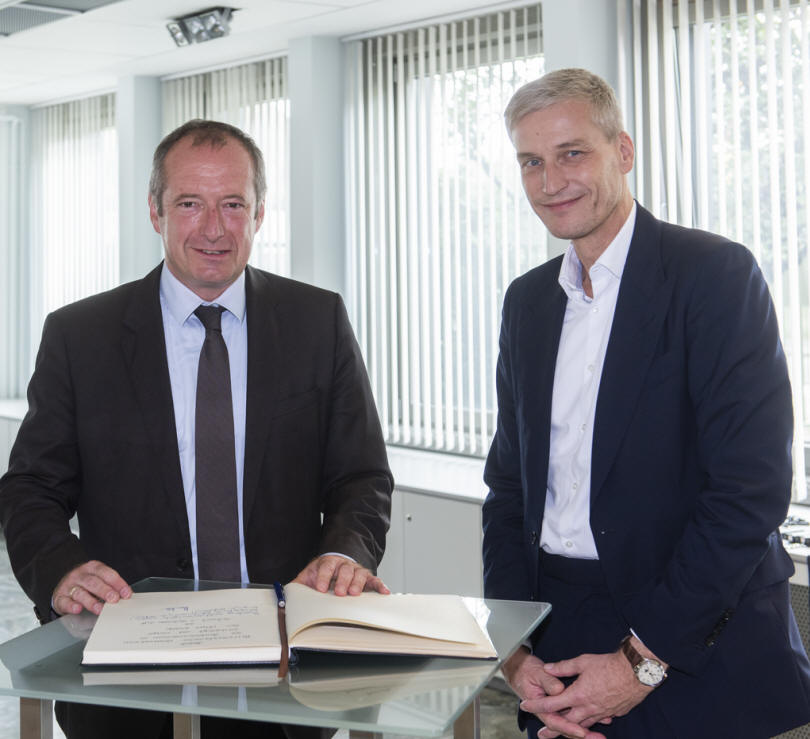
Oliver Wittke (l.) trägt sich neben Technikvorstand Dr.
Arnd Köfler in das Goldene Besucherbuch von thyssenkrupp
Steel Europe ein. Auf seiner CO2-Tour durch das
Ruhrgebiet informiert sich Wittke auch über die
Klimastrategien bei thyssenkrupp: CO2-Nutzung und
Vermeidung.
|
Klimastrategie von thyssenkrupp:
Parlamentarischer Staatssekretär Oliver Wittke informiert
sich
|
Duisburg, 3. Septembr 2019 -
Oliver Wittke, Parlamentarischer Staatssekretär beim
Bundesministerium für Wirtschaft und Energie, informiert
sich am 4. September über die Klimastrategie von
thyssenkrupp. Im Zentrum des Besuchs am Standort Duisburg
stehen das Wasserstoffprojekt der thyssenkrupp Steel
Europe AG und das Projekt Carbon2Chem. Beide Initiativen
sollen die CO2 Emissionen bei der Stahlproduktion
deutlich verringern und schließlich ganz vermeiden.
|
thyssenkrupp stellt Hightech-Bike aus Stahl her
und gewinnt Red Dot Design Award
|
Duisburg, 9. Juli 2019 -
thyssenkrupp Steel hat ein Hightech-Rennrad aus Stahl
entwickelt. steelworks heißt die neue
Ingenieurs-Meisterleistung, mit der der Stahlbereich von
thyssenkrupp den Best of the Best Red Dot Design Award in
der Kategorie Material & Surfaces in diesem Jahr gewonnen
hat.
Die Best of the Best Auszeichnung wird unter den
insgesamt rund 5.000 Einsendungen in 40 Kategorien nur
einmal je Kategorie verliehen. Im Zuge des Gewinns wird
steelworks nun ein Jahr lang im Red Dot Design Museum
ausgestellt.
Modernstes Material eröffnet neue Möglichkeiten Der
Hightech-Fahrradrahmen von thyssenkrupp ist aus
Dualphasen-Stahl gefertigt. Dabei handelt es sich um
modernsten, besonders beständigen Stahl, der eine höhere
Festigkeit und Steifigkeit als Aluminium besitzt und eine
Formgebung wie Carbon erlaubt.
Das verzinkte Stahlblech wird zunächst in zwei
Halbschalen gepresst und dann mit automatisierter und
dadurch hochpräziser 3D-Laserschweißtechnik
zusammengefügt. Diese Halbschalenfertigungstechnologie,
die sonst nur in der Hightech-Industrie zum Einsatz
kommt, ermöglicht nahezu unsichtbare Schweißnähte und
eine gleichbleibende High-End-Qualität bei der Produktion
der Fahrradrahmen.
Der Werkstoff Stahl zeigt hier eine völlig neue Variante
seiner konstruktiven Möglichkeiten. Die extreme
Steifigkeit des Stahlrahmens im Tretlagerbereich sichert
eine optimale Kraftübertragung und unterstützt den
Vortrieb. Gleichzeitig ermöglichen die hohe Flexibilität
im Sattelrohr sowie die eigene Dämpfung des Materials ein
ermüdungsfreies, komfortables Fahren.
Konventionsbruch für optimale Leistungsfähigkeit und mehr
Komfort Im Normalfall werden heutige Fahrradrahmen aus
Aluminiumrohren oder Kohlefaserlaminaten gefertigt, um
eine hohe Steifigkeit zu erreichen, wodurch allerdings
zwangsläufig der Komfort leidet. steelworks setzt genau
an diesem Punkt an.
„Die vielseitigen Eigenschaften von Stahl haben uns
inspiriert. Ohne die hervorragenden Umformeigenschaften
des Stahls bei gleichzeitig hoher Festigkeit wäre die
bionische Gestaltung des Sattelrohres nicht möglich
gewesen“, sagt Jia-Uei Chan, Projektleiter von
steelworks. Mit Stahlfeinblech und modernsten
Fertigungsverfahren bricht steelworks mit den üblichen
Konventionen des Fahrradrahmenbaus und vereint so die
sonst gegensätzlichen Design-Ansprüche Steifigkeit und
Komfort. Kaufen kann man das Fahrrad ab Spätsommer 2019.
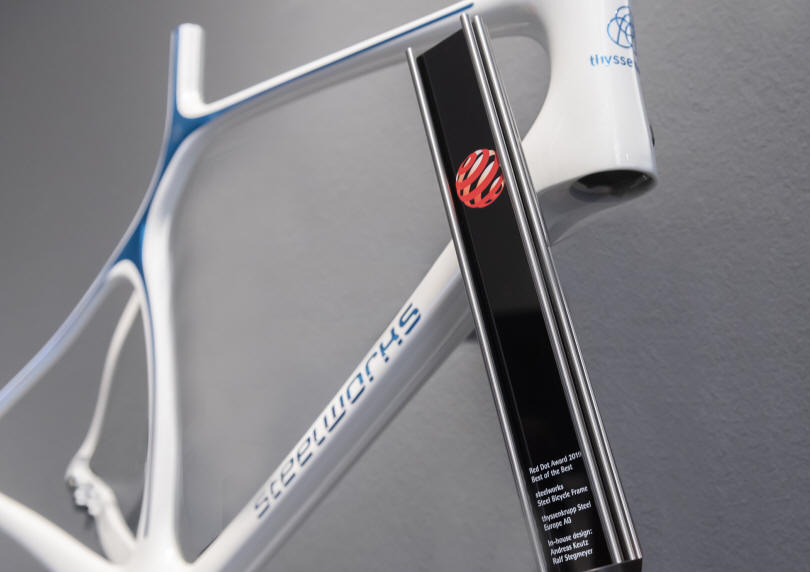
thyssenkrupp Steel hat ein Hightech-Rennrad aus Stahl
entwickelt: steelworks heißt die neue
Ingenieurs-Meisterleistung, mit der der Stahlbereich von
thyssenkrupp den Best of the Best Red Dot Design Award in
der Kategorie Material & Surfaces in diesem Jahr gewonnen
hat.
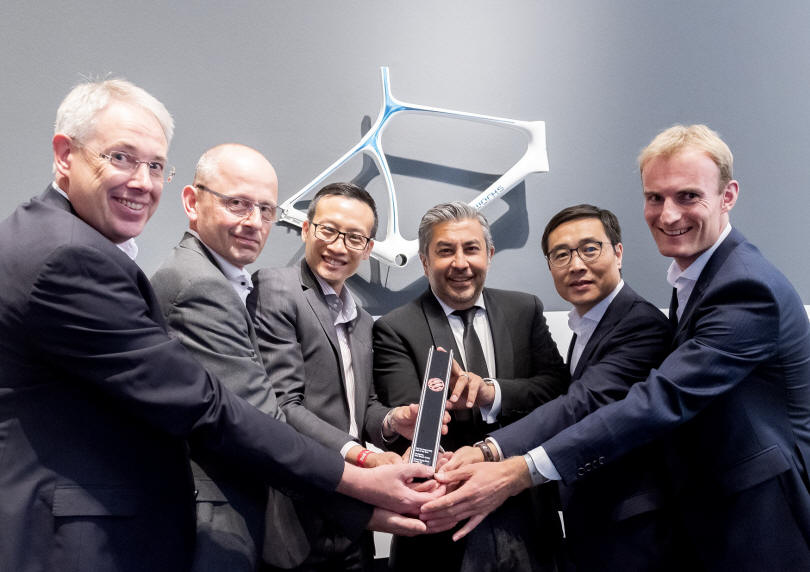
Die Best of the Best Auszeichnung wird unter den
insgesamt rund 5.000 Einsendungen in 40 Kategorien nur
einmal je Kategorie verliehen. Über den Preis freuten
sich am Montag für thyssenkrupp (v.l.n.r.) Dr. Hans-Peter
Schmitz, Ralf Stegmeyer (beide aus dem Bereich Forschung
und Entwicklung), Jia-Uei Chan (Projektleiter
steelworks), Premal Desai (Vorstand thyssenkrupp Steel),
Dr. Yu Sun (Forschung und Entwicklung) und Andreas Keutz
(Projektmanager Automobil-Kunden)
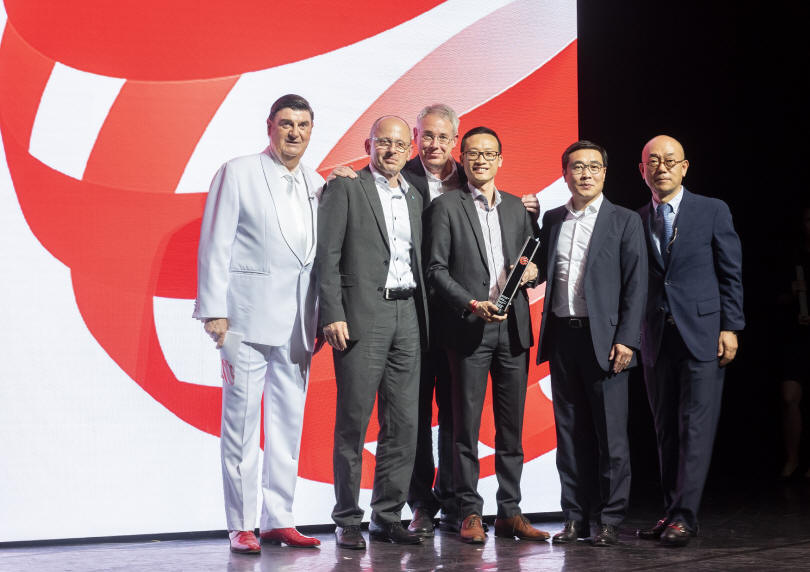
Ingenieurs-Meisterleistung aus dem Hause thyssenkrupp
wurde mit dem Best of the Best Red Dot Design Award in
der Kategorie Material & Surfaces am Montag
ausgezeichnet. Prof. Dr. Peter Zec (ganz links) ist
Initiator und CEO von Red Dot und beglückwünscht
gemeinsam mit Prof. Dr. Ken Nah (Jury) die Vertreter von
thyssenkrupp (v.l.n.r.) Ralf Stegmeyer, Dr. Hans-Peter
Schmitz (beide aus Forschung und Entwicklung), Jia-Uei
Chan (Projektleiter steelworks), Dr. Yu Sun (Forschung
und Entwicklung).
|
Demonstrationsflug: Autonome
Transportdrohne beschleunigt Anlieferung von Laborproben
bei thyssenkrupp Steel um rund 70 Prozent
|
Duisburg, 21. Mai 2019 - Er ist ein
echter Überflieger: der Flugroboter delivAIRy®, der heute
auf dem Werkgelände von thyssenkrupp in Duisburg alle
Blicke auf sich zog. Ein leises Surren, dann startete die
Transportdrohne im Beisein von NRW-Verkehrsminister
Hendrik Wüst zu ihrem ersten offiziellen
Demonstrationsflug durch. In rasantem Tempo schwebte sie
über dem Hüttenwerk davon und lieferte wenige Minuten
später eine Box mit Laborproben sicher und
vollautomatisiert auf dem Werksgelände ab.
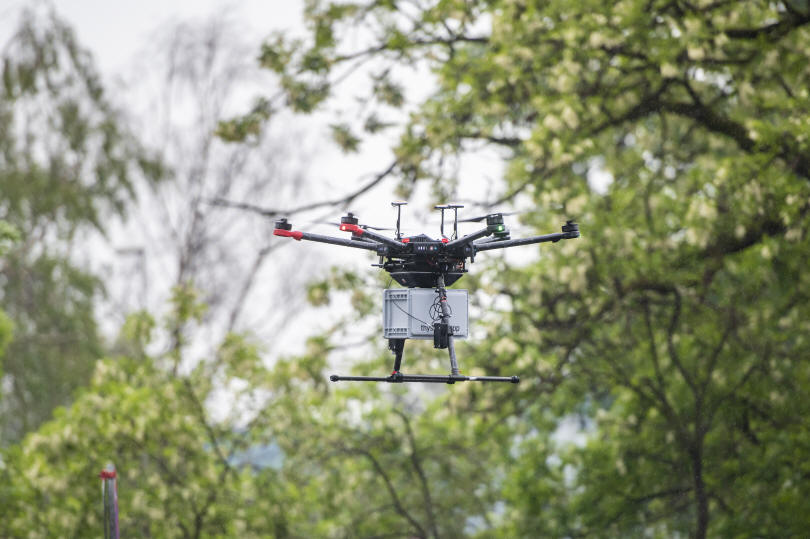
„Der Probeflug einer autonom fliegenden Transportdrohne
zeigt, dass wir in NordrheinWestfalen gute
Voraussetzungen haben, bei der Entwicklung innovativer
Technologien vorne dabei zu sein. Wir haben die
Kompetenzen in Wissenschaft und Wirtschaft und optimale
Testbedingungen. Was hier im kleineren Umfang getestet
wird, ist wegweisend für die Mobilität in unseren
Städten. In einem solch bevölkerungsstarken und
verkehrsreichen Land wie Nordrhein-Westfalen ist es
richtig, mit dem Luftraum die dritte Dimension der
Mobilität mitzudenken. Die Nutzung des Luftraums eröffnet
uns Optionen für neue Mobilitätsangebote,“ sagte
NRW-Verkehrsminister Hendrik Wüst.
Zweimal täglich macht sich bislang ein Werksarbeiter von
thyssenkrupp Steel per Pkw auf den Weg, um kleine Dosen
mit Rohstoffen wie Eisenerz oder Kokskohle von der
Rohstoffaufbereitung im Werkhafen Schwelgern ins
Zentrallabor zu bringen. Dort wird die Qualität der
angelieferten Ausgangsstoffe für die Stahlproduktion
anhand von Stichproben kontrolliert. Auf der Strecke zum
Labor muss der Fahrer mehrere unbeschrankte Bahnübergänge
überqueren. Das ist nicht nur zeitraubend und teuer,
sondern birgt auch Unfallrisiken.
„Projekte wie bei thyssenkrupp machen sehr deutlich,
welchen Mehrwert Drohnen in der Hand von professionellen
Nutzern haben“, sagte der Koordinator der Bundesregierung
für die Deutsche Luft- und Raumfahrt, Thomas Jarzombek.
„Überall in Deutschland etablieren Innovatoren ganz neue
Geschäftsmodelle rund um das Thema Drohnen. Die
Bundesregierung unterstützt diesen Zukunftsmarkt, z.B.
durch die Förderung von Forschung und Entwicklung. Aber
auch die regulatorischen Rahmenbedingungen müssen
stimmen.“
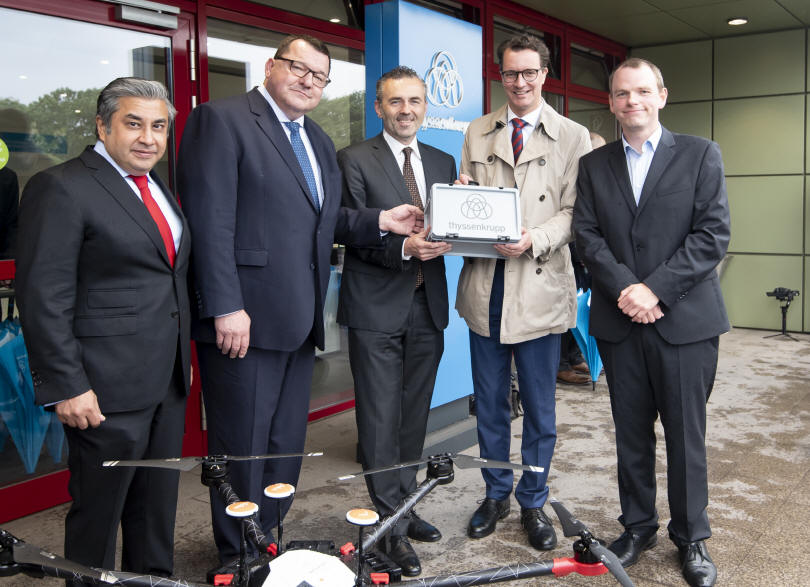
Verkehrsminister Hendrik Wüst (4. von
links) erhält die ersten von der Transportdrohne
gelieferten Rohstoffproben als Geschenk.
Von links: Premal A. Desai, Vorstandsmitglied – Finanzen,
thyssenkrupp Steel Europe AG, Andreas J. Goss,
Vorsitzender des Vorstands thyssenkrupp Steel Europe AG,
Thomas Jarzombek, Koordinator der Bundesregierung für die
Deutsche- Luft- und Raumfahrt, NRW Verkehrsminister
Hendrik Wüst, Dr. Thomas Lostak, Projektleiter)
Ein „hochfliegender“ Plan Um den Laborprobentransport zu
beschleunigen, sicherer zu machen und zusätzlich auch
noch den Werksverkehr zu entlasten, entwickelte
thyssenkrupp Steel einen buchstäblich hochfliegenden
Plan: die Anlieferung der Laborproben auf dem Luftweg.
Als Partner fand sich die doks.innovation GmbH, die den
autonomen Flugroboter delivAIRy® mit 1,20 Meter
Spannweite, einer Tragkraft von 4,5 Kilo und einer
patentierten Technologie für die autonome Lastaufnahme
entwickelt hat.
„Auch dieses Projekt ist eines von vielen, mit denen wir
das Stahlwerk der Zukunft bauen: moderner, digitaler und
nachhaltiger. Dabei forcieren wir
Digitalisierungsprojekte nicht um ihrer selbst willen,
sondern immer dann, wenn sie uns konkrete Fortschritte
bringen. Die Transportdrohne dafür ein exzellentes
Beispiel“, sagte der Vorstandsvorsitzende von
thyssenkrupp Steel Europe, Andreas Goss. Für die 2,2
Kilometer lange Strecke braucht delivAIRy® nur rund sechs
Minuten, während der Pkw bis zu einer viertel Stunde oder
länger braucht – je nach Witterung und Verkehrslage.
Insgesamt beschleunigt sich der Lieferprozess so um mehr
als die Hälfte.
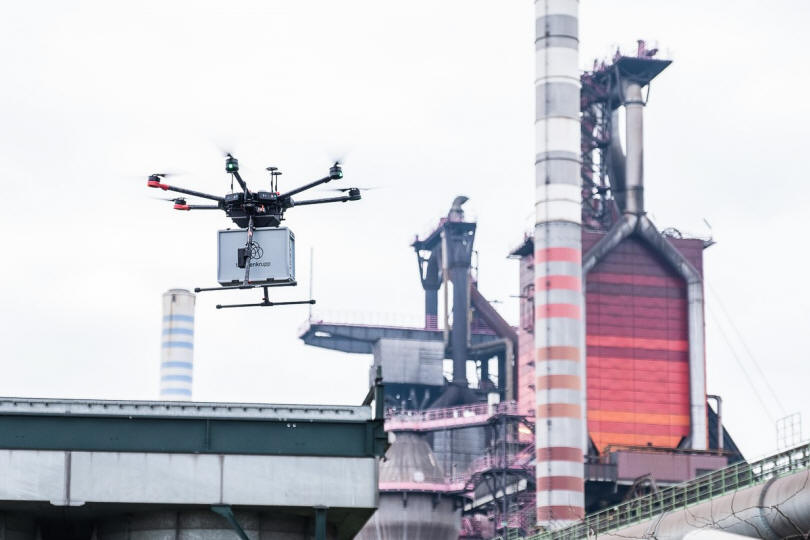
Bewegungen immer im Blick Über einen zentralen Leitstand
haben zwei eigens ausgebildete Mitarbeiter die Bewegungen
der Drohne immer im Blick. So wissen sie stets genau, wo
sich der Flugroboter befindet und können ihn auf sechs
definierten Notfalllandeplätzen entlang der Strecke
jederzeit zum Stehen bringen. Fallschirme, eine Redundanz
der Flugsteuerung und eine Kombination aus optischer
Navigation und Navigation via GPS sorgen für zusätzliche
Sicherheit. Für die sechsmonatige Pilotphase und den
Flugbetrieb sind entsprechende Fluggenehmigungen durch
die Landesluftfahrtbehörde Nordrhein-Westfalen nötig; die
Verfahren dazu laufen. Wenn sich der autonome Flugroboter
dann beim Laborprobentransport bewährt, könnte er in
Zukunft auch in anderen Bereichen der internen Logistik
zum Einsatz kommen.
„Die Drohne lässt sich individuell per App anfordern. Die
Auslieferung zeitkritischer Sendungen auf dem
Werksgelände könnte man damit voll automatisieren und
digitalisieren“, erklärte Projektleiter Dr. Thomas
Lostak. „Das Projekt kommt sehr gut bei den Kolleginnen
und Kollegen an.“ Die abstrakte Thematik der
Digitalisierung werde durch den Drohneneinsatz
eindrucksvoll greifbar. Das liefere frischen Rückenwind
für weitere Digitalisierungsprojekte.
|
|
Abgesagte Fusion von tks und Tata birgt Risiken
für den Standort Duisburg
|
Duisburg, 10. Mai 2019 - Mit
großer Überraschung hat die Gesellschaft für
Wirtschaftsförderung Duisburg mbH (GFW Duisburg) die
Absage der Fusion von thyssenkrupp und Tata Steel
aufgenommen. „Das kommt überraschend und ist keine gute
Nachricht für Duisburg“, sagt Andree Haack,
Wirtschaftsdezernent der Stadt Duisburg. Eigentlich war
die Fusion für dieses Jahr angekündigt, wurde aber jetzt
abgesagt, da die Europäische Kommission dem Vorhaben sehr
kritisch gegenübersteht.
„Der internationale Stahlmarkt ist durch subventionierte
Produktion in anderen Ländern enorm unter Druck geraten.
Ohne die Fusion mit Tata Steel ist es nur logisch, dass
thyssenkrupp jetzt agieren muss. Der angekündigte
Stellenabbau hätte vermieden werden können“, meint Haack
und GFW-Geschäftsführer Ralf Meurer ergänzt, dass die
Stahlproduktion in anderen Ländern häufig nicht so hohen
Qualitäts-, Umwelt- und Sozialstandards unterliegt, wie
in Deutschland. Beide sind sich aber auch einig, dass der
Stahlstandort Duisburg nach wie vor aufgrund seiner
Lagevorteile und dem hohen technischen Standard nicht
gefährdet ist.
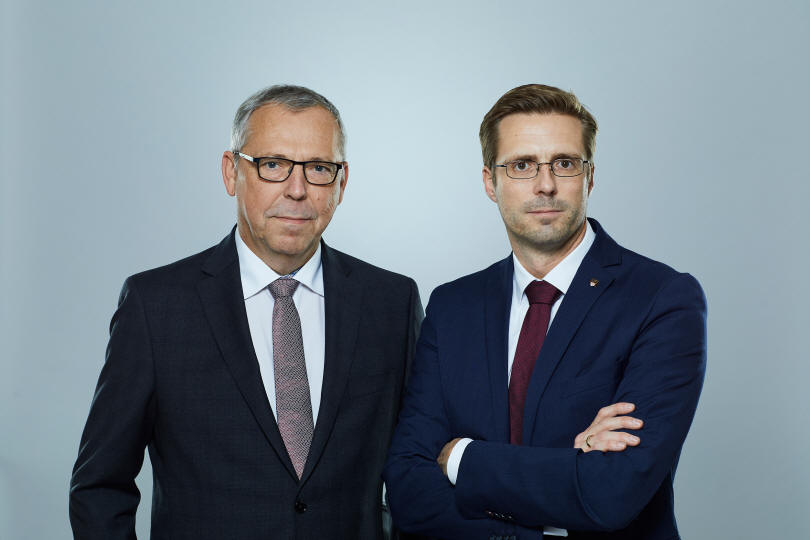
Andree Haack, Wirtschaftsdezernent (rechts) und
GFW-Mitgeschäftsführer, sowie GFW-Geschäftsführer Ralf
Meurer; Urheberin: Jacqueline Wardeski -
Nutzungsrechte: GFW Duisburg
|
|
Safety first: thyssenkrupp Steel kooperiert
beim Arbeitsschutz mit der Grubenrettung Herne
|
Duisburg, 27. April 2019 - Der
28. April ist der Welttag für Sicherheit und Gesundheit am
Arbeitsplatz. Der Stahlbereich von thyssenkrupp
stellt jedoch nicht nur an diesem Tag höchste Anforderungen
an die Sicherheit der Mitarbeiterinnen und Mitarbeiter und
widmet daher dem Weltsicherheitstag auch in diesem Jahr
wieder fast eine ganze Woche. In dieser Zeit gibt es viele
Aktionen, die auf das Thema aufmerksam machen. Dass am Ende
des Tages die gesamte Belegschaft gesund nach Hause geht,
hat immer höchste Priorität.
Kooperation mit dem
Grubenrettungswesen Herne hilft Unfälle zu vermeiden.
Bei der kontinuierlichen
Verbesserung der Sicherheit am Arbeitsplatz setzt der
Arbeitsschutz bei thyssenkrupp auf die aktive Einbeziehung
aller Mitarbeiterinnen und Mitarbeiter. Denn jede praktische
Erfahrung hilft, die Lösung für ein Problem bereits bei der
Planung zu erarbeiten. Michael Cremer ist Teil dieses
Prozesses. Er ist zuständig für die mechanische
Instandhaltung in der Kokerei Schwelgern. Die
Atemschutzmannschaft der Kokerei muss immer wieder größere
Gasarbeiten durchführen. Dabei trägt das Team schwere
Atemschutzgeräte auf dem Rücken und Masken, die das
Sichtfeld einschränken.
Für die Arbeit unter solchen Bedingungen ist viel Erfahrung
nötig. Doch auf dem Gelände der Kokerei gibt es keinen
geeigneten Trainingsplatz, um diese Erfahrung unter
kontrollierten Bedingungen zu machen. Daher arbeitet die
Atemschutzmannschaft mit dem Grubenrettungswesen in Herne
zusammen. „Die Zusammenarbeit hilft uns sehr, denn so kann
das Team mit der Originalausrüstung trainieren und die
nötige Erfahrung sammeln“, sagt Michael Cremer. Durch das
praxisnahe Sicherheitstraining werden alle Mitarbeiterinnen
und Mitarbeiter fit für ihre Einsätze. So können Unfälle
aufgrund mangelnder Übung und Erfahrung vermieden werden.
Langfristiges Ziel: Null Unfälle
Das langfristige Ziel bei
thyssenkrupp lautet: Null Unfälle. Um dieses Ziel zu
erreichen, muss der Arbeitsschutz integraler Bestandteil
aller Betriebsabläufe sein. Sicherheit ist zu jeder Zeit
wichtiger als Schnelligkeit. Damit dieses Verständnis von
Sicherheit überall zum Alltag wird, braucht es allerdings
Geduld. „Eine neue Sicherheitskultur im Unternehmen
zu verankern, braucht vor allem eines: Zeit. Diese Zeit
müssen wir uns nehmen, denn wir wollen keine halben Sachen
machen. Wir wollen es richtigmachen“, sagt Dr. Sabine
Maaßen, Arbeitsdirektorin bei thyssenkrupp Steel.
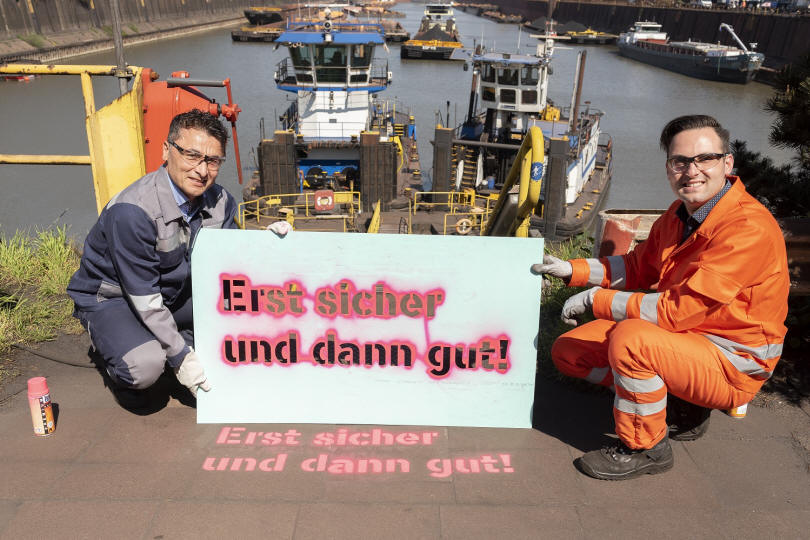
Der Stahlbereich von thyssenkrupp stellt höchste
Anforderungen an die Sicherheit der Mitarbeiter und macht
deshalb aus dem Weltsicherheitstag am 28. April unter dem
Motto „Erst sicher und dann gut!“ wieder fast eine ganze
Woche. Vom 25.4. bis zum 30.4. gibt es viele Aktionen an
allen Standorten.
„Safety
first“ – dafür engagiert sich auch thyssenkrupp Steel
Mitarbeiter Michael Cremer.
Mit seinem Team übt er deshalb den Einsatz für Arbeiten mit
Atemschutzgeräten, die zum Beispiel an der weltgrößten
Kokerei auf dem Werkgelände von thyssenkrupp in
Duisburg-Schwelgern anfallen.
Für bestmögliche Trainingsergebnisse wird dafür mit dem
Grubenrettungswesen Herne kooperiert.
|
|
Wasserstoff statt Kohle
|
thyssenkrupp Steel
startet wegweisendes Projekt für eine klimafreundliche
Stahlproduktion am Standort Duisburg
Landesregierung fördert erste Testphase im Duisburger
Stahlwerk
Projekt ist die erste Förderung im Rahmen der Initiative
IN4climate.NRW
Projektpartner Air Liquide liefert den Wasserstoff
Duisburg, 16. April. NRW-Wirtschafts- und Digitalminister
Prof. Dr. Andreas Pinkwart übergab am Montag einen
Förderbescheid des Landes, um die Dekarbonisierung der
Produktion beim größten deutschen Stahlhersteller durch den
Einsatz von Wasserstoff zu unterstützen.
Damit wird zugleich die umfassende Transformation des
Standortes hin zu einer klimafreundlichen Stahlproduktion
weiter vorangetrieben. thyssenkrupp Steel verfolgt das
langfristige Ziel, die bislang bei der Produktion
anfallenden CO2-Emissionen bis 2050 um mindestens 80 Prozent
zu verringern. Das nun beginnende Projekt wird im Rahmen der
vor kurzem von der Landesregierung gestarteten Initiative
IN4climate.NRW gefördert.
Wirtschafts- und Digitalminister Prof. Dr. Andreas Pinkwart:
„Es ist mir eine besondere Freude, heute den Förderbescheid
für das erste Projekt der Initiative IN4climate.NRW
übergeben zu können, mit dem wir einen wichtigen Schritt in
Richtung einer klimaneutralen Industrie gehen. Um
ambitionierten Klimaschutz mit einer auch in Zukunft global
wettbewerbsfähigen Industrie zu erreichen, muss es
Innovationen bei industriellen und energieintensiven
Prozessen wie der Stahlherstellung geben. Diesen
Transformationspfad möchten wir als Land Nordrhein-Westfalen
gemeinsam mit der Industrie und der Wissenschaft gehen. Das
Pilotprojekt zeigt, dass unsere Initiative IN4climate.NRW
bereits erste Früchte trägt. Ich bin froh, dass wir
thyssenkrupp Steel, Air Liquide und das BFI hier als
innovative Partner an unserer Seite haben“. Air Liquide, ein
Weltmarktführer für Industriegase, liefert den für das
Projekt benötigten Wasserstoff.
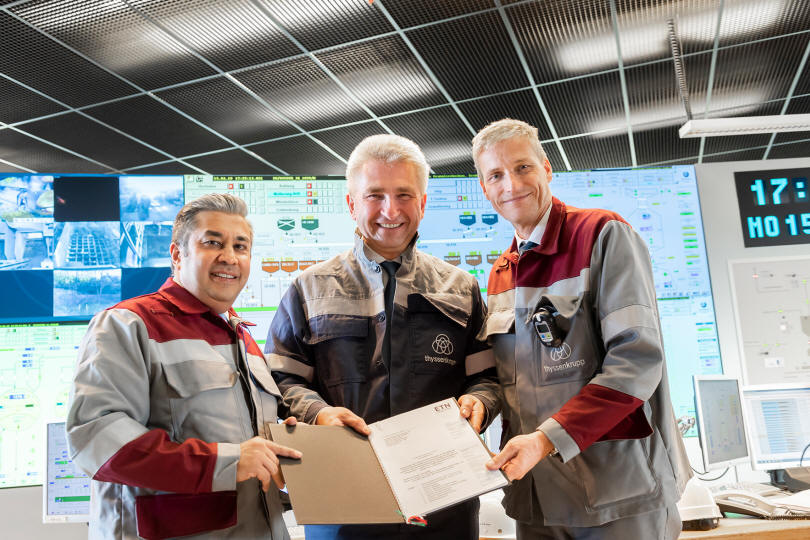
Wirtschafts- und
Digitalminister Prof. Dr. Andreas Pinkwart (Mitte)
überreicht den Förderbescheid des Landes NRW an Premal
Desai, Finanzvorstand thyssenkrupp Steel (links) und Dr.
Arnd Köfler, Technikvorstand thyssenkrupp Steel
Wasserstoffprojekt als weiterer Meilenstein auf dem Weg zu
einer klimafreundlichen Stahlerzeugung thyssenkrupp bekennt
sich zu den Pariser Klimaschutzzielen. Bei der notwendigen
Umstellung seiner Stahlproduktion geht das Unternehmen dabei
technologieoffen vor und nutzt verschiedene, sich ergänzende
Ansätze. So können mit dem bereits erfolgreich gestarteten
Projekt Carbon2Chem in der Stahlproduktion entstehende
Treibhausgase in Chemieprodukte umgewandelt werden und sind
so als wertvolle Rohstoffe nutzbar.
Das Wasserstoffprojekt am Hochofen beschreitet einen
weiteren Technologiepfad: Hier wird vermieden, dass
schädliche Treibausgase überhaupt entstehen. Dies geschieht
dadurch, dass ein Teil des im Hochofen als Reduktionsmittel
eingesetzten Kohlenstaubes durch das Einblasen von
Wasserstoff ersetzt wird.
„Mit dem Einsatz von Wasserstoff an unserem Hochofen 9
arbeiten wir weiter konsequent an der Umstellung unserer
Produktionsprozesse. Unser Ziel ist eine nahezu CO2-neutrale
Stahlerzeugung. Dies wird ein langer und kostenintensiver
Prozess, auf dem wir heute einen weiteren Schritt
vorangehen“, erläutert Arnd Köfler, Produktionsvorstand von
thyssenkrupp Steel Europe.
„Wie testen in dieser ersten Projektphase in den nächsten
Monaten zunächst den Einsatz von Wasserstoff an einer von 28
Blasformen eines Hochofens. Das ist ein Novum und so bislang
in der Industrie noch nicht umgesetzt worden. Wir werden die
Ergebnisse dieser Testphase genau analysieren und wollen
dann in einer zweiten Projektphase den gesamten Hochofen auf
diese Weise umstellen,“ ergänzt Köfler.
„Theoretisch ist so ein Einsparpotenzial von rund 20 Prozent
CO2 an dieser Stelle des Produktionsprozesses möglich. Wir
sind sehr dankbar, dass die Landesregierung uns hier mit
einer Förderung im Rahmen von IN4climate.NRW unterstützt.
Mit Air Liquide für die Wasserstoffversorgung und dem BFI
als wissenschaftlichen Begleiter des Projekts, haben wir
genau die richtigen Partner an unserer Seite.“
Wasserstoff: Schlüssel zu einer klimafreundlichen Zukunft
Wasserstoff ist ein zentraler Treiber für die Erreichung von
Klimaambitionen, da er am Einsatzort keine klimaschädlichen
Emissionen verursacht. Er kann in flüssiger oder gasförmiger
Form mit hoher Energiedichte gespeichert und transportiert
werden und bietet so viele Einsatzmöglichkeiten. Aufgrund
seiner Vielseitigkeit spielt Wasserstoff eine Schlüsselrolle
beim Übergang zu einem sauberen, kohlenstoffarmen
Energiesystem. In der Stahlherstellung kann Wasserstoff als
emissionsfreies Reduktionsmittel für das Eisenerz verwendet
werden.
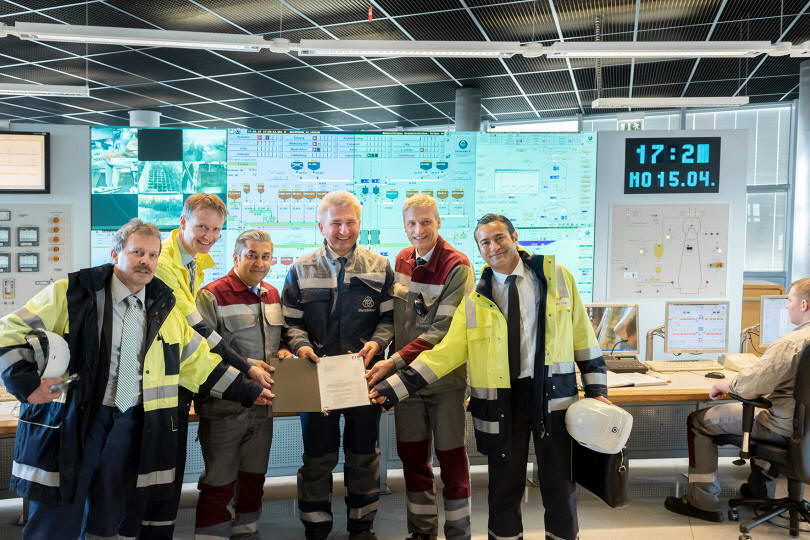
Gemeinschaftsprojekt mit dem Ziel einer klimafreundlichen
Stahlproduktion. Von links: Michael Hensmann (BFI); Robert
van Nielen, Geschäftsführer Large Industries bei Air
Liquide; Premal Desai, Finanzvorstand thyssenkrupp Steel
Europe; Dr. Arnd Köfler, Technikvorstand thyssenkrupp Steel;
Gilles Le Van, Geschäftsführer Air Liquide Deutschland.
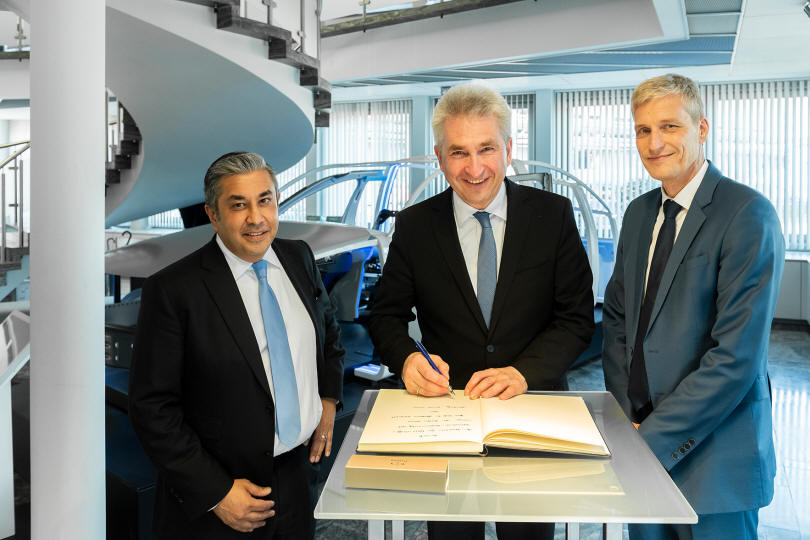
Eintrag in
das Goldene Buch von thyssenkrupp Steel. Von links: Premal
Desai, Finanzvorstand thyssenkrupp Steel Europe;
Wirtschafts- und Digitalminister Prof. Dr. Andreas Pinkwart;
Dr. Arnd Köfler, Technikvorstand thyssenkrupp Steel
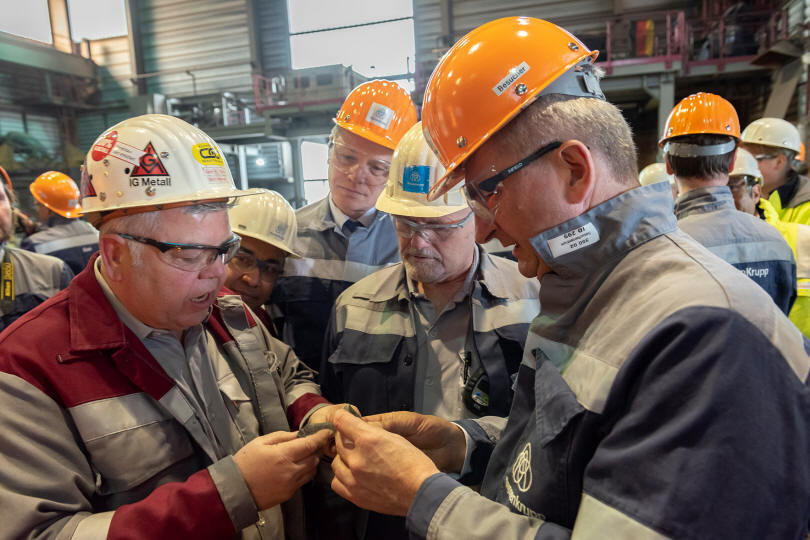
Roheisenprobe am Hochofen: Horst Gawlik, Stellv.
Betriebsratsvorsitzender thyssenkrupp Steel Europe mit
Wirtschafts- und Digitalminister Prof. Dr. Andreas Pinkwart
Air Liquide, Projektpartner für das nun beginnende
Wasserstoffprojekt bei thyssenkrupp Steel, verfügt über
Expertise in der gesamten Wasserstoff-Wertschöpfungskette
von der Produktion über die Speicherung bis hin zur
Entwicklung von Endverbraucheranwendungen.
Gilles Le Van, Vorsitzender der Geschäftsführung von Air
Liquide Deutschland, sagte: “Hier in Duisburg wird nun ein
bedeutendes Kapitel der industriellen Entwicklung
aufgeschlagen: die schrittweise und nachhaltige
Dekarbonisierung der Stahlerzeugung. Wir freuen uns sehr, an
diesem Vorhaben mitzuwirken - zuerst im Testbetrieb, später
im größeren Maßstab. Unser langjähriger Kunde und Partner
thyssenkrupp Steel stellt wiederholt unter Beweis, wie eine
innovative Industrie erfolgreich mit Wettbewerbsfähigkeit
und Klimaschutz einhergehen kann.”
thyssenkrupp Steel gehört zu den weltweit führenden
Anbietern von Qualitätsflachstahl. Mit r und 27.000
Mitarbeitern liefert das Unternehmen hochwertige
Stahlprodukt e für innovative und anspruchsvolle Anwendungen
in verschiedensten Industriezweigen.
Air Liquide ist ein weltweit führender Anbieter von Gasen,
Technologien und Services für Industrie und Gesundheit, ist
in 80 Ländern mit rund 66.000 Mitarbeitern vertreten und
erzielte 2018 einen Umsatz von rund 21 Milliarden Euro. Das
Unternehmen beliefert drei Viertel der Industrieunternehmen
im DAX und bildet so eine wichtige Stütze der deutschen
Wirtschaft. Air Liquide Deutschland ist in NRW zu Hause und
in Branchenverbänden wie dem Verband der Chemischen
Industrie (VCI) aktiv. https://www.airliqui de.com/
Mit der Initiative „IN4climate.NRW“ unterstützt die
Landesregierung die notwendigen Transformationsprozesse in
der Industrie. Expertinnen und Experten aus Wirtschaft,
Wissenschaft und Verwaltung arbeiten derzeit an Strategien
und Lösungen, wie die Industrie ihre Wettbewerbsfähigkeit
erhalten, zusätzliches Wachstum erzeugen und zur Erreichung
der Pariser Klimaschutzziele beitragen kann.
https://www.in4climate.nrw/
|
|
Jubiläum bei thyssenkrupp in Duisburg:
Gießwalzanlage wird 20 Jahre
|
Ein Meilenstein in der
Stahlherstellung erweist sich als Investition in die Zukunft
Duisburg, 5. April 2019 - Anfang
April 1999 ging im Duisburger Werk von thyssenkrupp Steel
die erste Gießwalzanlage (GWA) in einem integrierten
Hüttenwerk in Betrieb – ein Meilenstein in der
Flachstahlherstellung. In der GWA wird in einem
durchgängigen Prozess flüssiger Rohstahl gegossen und direkt
gewalzt.
Heute produzieren an der Anlage 230 Mitarbeiter in fünf
Schichten so viele Tonnen „Warmband“, dass man mit diesem
Stahl theoretisch rund 12.000 Mittelklassewagen pro Tag
herstellen könnte. Die Investition von umgerechnet 300
Millionen Euro hat sich als weitsichtig und lohnend für den
Standort erwiesen: Mit der neuen Anlage werden höchste
Stahlqualitäten u.a. für die Automobil- und
Hausgeräteindustrie produziert.
Weltweit erste Gießwalzanlage
in einem Hüttenwerk
Mit einer Länge von 450 Metern ist
die Gießwalzanlage (GWA) ein Kernstück im Duisburger Werk.
Sie produziert aus flüssigem Rohstahl sogenanntes
„Warmband“, aufgewickeltes Stahlblech, das im heißen Zustand
gewalzt wurde. Aus diesem Warmband werden nach mehreren
Weiterverarbeitungs- und Veredelungsstufen zum Beispiel
Teile für Autos, Möbel oder Elektromotoren hergestellt.
„Unsere GWA wurde als weltweit erste ihrer Art in einem
integrierten Hüttenwerk gebaut“, sagt Dr. Carmen Ostwald
stolz, die seit 2016 die Gießwalzanlage leitet. „Mit der GWA
konnten wir den Fertigungsprozess deutlich kürzen, das spart
fast zwei Drittel der Energie und CO2, weil das
Abkühlen der aus dem Rohstahl gegossenen Brammen und ihr
Wiederaufheizen für den Walzvorgang wegfallen. Das Verfahren
ermöglicht zudem die Produktion höchster Stahlqualitäten.“
Zwei Schritte in einem
durchgehenden Prozess
Als die GWA 1999 nach zwei Jahren
Bauzeit in Betrieb ging, war die Technologie noch neu. Zwei
bis dahin getrennte Verfahren in der Stahlherstellung wurden
in einen durchgehenden Prozess zusammengefügt: das Gießen
des flüssigen Rohstahls zu Blöcken, die das Vormaterial für
Bleche und Bänder darstellen (Brammen), und das Walzen. Die
Entwicklung von Gießwalzanlagen gilt als Technologiesprung
in der Flachstahlproduktion.
„Mit dieser Investition haben unsere Vorgänger etwas Neues
gewagt – und die Entscheidung war richtig“, sagt Dr.
Heribert Fischer, Technischer Vorstand bei thyssenkrupp
Steel. „Mit der Zusammenlegung von zwei Prozessschritten in
einer Anlage haben wir vor 20 Jahren schon in die Stahlgüten
von heute investiert. Damit bieten wir unseren Kunden
höchste Qualität für ihre Produkte.“
Durch die gleichmäßige Temperaturverteilung während des
durchlaufenden Prozesses – die Brammen werden auf einer
konstanten Walztemperatur von 1.150 Grad gehalten – sind
Festigkeit und Dehnung des Stahls viel gleichmäßiger als in
herkömmlichen Verfahren. Zugleich können die Bleche sehr
dünn gewalzt werden – bis zu 0,8 Millimeter; das entspricht
ungefähr 8 Papierseiten.
Auf dieser Anlage werden auch heute ständig neue
Stahlqualitäten entwickelt, mit denen thyssenkrupp Steel
einen wichtigen Beitrag zum Erfolg seiner Kunden aus
Automobil-, Elektro- und Bau-Industrie und zur Sicherung
vieler Arbeitsplätze leistet.
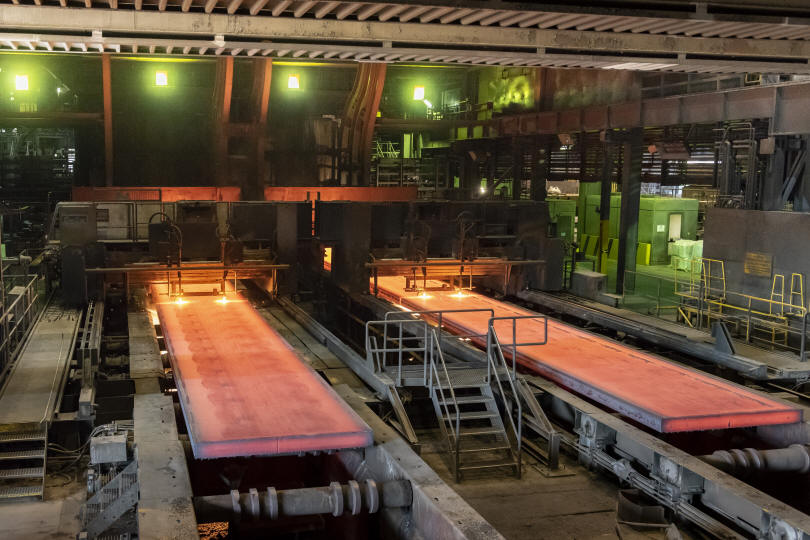
Als weltweit erste ihrer Art
wurde die Gießwalzanlage von thyssenkrupp Steel in einem
integrierten Hüttenwerk gebaut und so konstruiert, dass der
flüssige Rohstahl parallel in zwei Strängen gegossen werden
kann. Zwei bis dahin getrennte Verfahren in der
Stahlherstellung wurden in einen durchgehenden Prozess
zusammengefügt: das Gießen des flüssigen Rohstahls zu
Blöcken, die das Vormaterial für Bleche und Bänder
darstellen (sogenannte Brammen), und das Walzen.
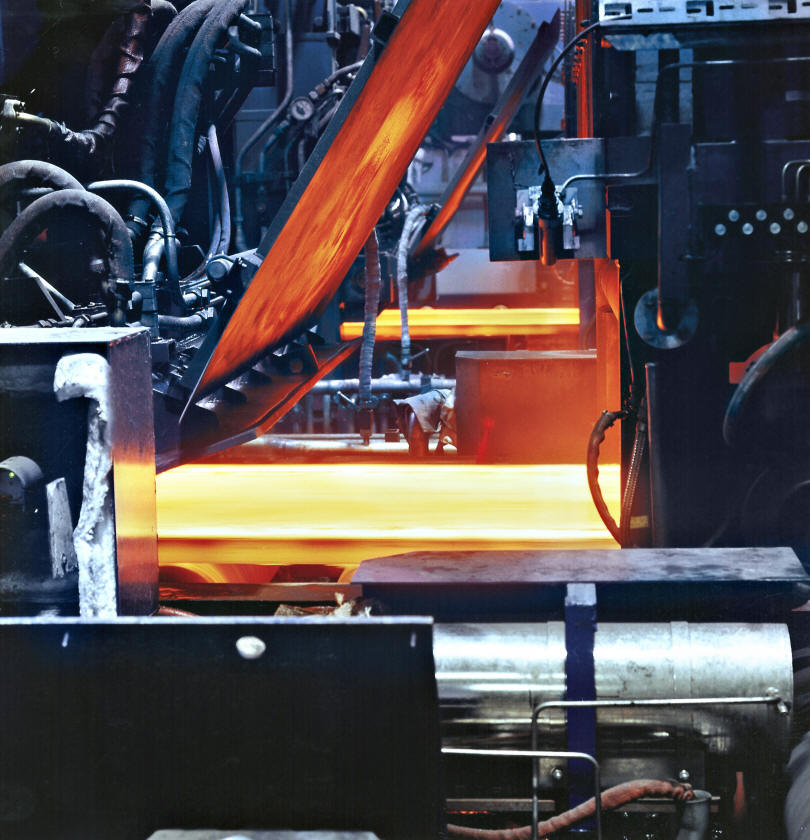
Die Stahlblöcke werden bei einer konstanten Walztemperatur
von 1.150 Grad zu dünnen Blechen gewalzt. Durch die
Besonderheiten der Gießwalzanlage sind Dicken von bis zu 0,8
Millimetern möglich; das entspricht ungefähr 8 Papierseiten.
|
|
Leistungswandel als Chance
|
thyssenkrupp Steel erprobt
mit Partner im Projekt „TErrA“ neue Wege der
überbetrieblichen Zusammenarbeit
Duisburg, 22. Februar 2019 - Die
gleiche Arbeit von der Ausbildung bis zur Rente: Wenn die
körperliche Belastung hoch ist oder sich Anforderungen an
Qualifikationen – Stichwort Digitalisierung – wandeln, geht
die Vorstellung von der lebenslangen Beschäftigung im einmal
gewählten Beruf nicht immer auf: „Leistungswandlung muss aber
nicht gleichbedeutend mit Leistungsausfall sein“, erklärt Dr.
Veit Echterhoff, Leiter Human Resources Center bei
thyssenkrupp Steel. „Kann ein Mitarbeiter seine bisherige
Tätigkeit, beispielsweise aus gesundheitlichen Gründen, nicht
mehr ausführen, dann bedeutet das keinesfalls automatisch den
Verlust seiner Arbeitsfähigkeit oder seiner fachlichen
Kompetenz.“
Prävention als Schlüssel zur
erfolgreichen Veränderung
Stichwort Leistungswandel: Wie
Unternehmen diese Herausforderung erfolgreich meistern
können, war Thema des Forschungsprojekts „TErrA –
Tätigkeitswechsel zum Erhalt der Arbeitsfähigkeit in
regionalen Netzwerken“, dessen Ergebnisse nun in Dortmund
vorgestellt wurden. Auch thyssenkrupp Steel hatte daran
teilgenommen und seine Erfahrungen eingebracht: Bausteine wie
Gesundheitsmaßnahmen, Inklusionsprojekte und Programme zur
beruflichen Weiterentwicklung zielen bereits heute darauf ab,
die Beschäftigten präventiv zu unterstützen. „Aus diesem
Grund bestärken wir die Beschäftigten darin, uns ihre
Probleme frühzeitig mitzuteilen“, erläutert Veit Echterhoff.
Wird es absehbar, dass eine Tätigkeit nicht mehr ausgeübt
werden kann, muss man gemeinsam eine Alternative finden. Dazu
hat thyssenkrupp Steel mit dem unternehmenseigenen
Fachbereich Inklusion ein breit aufgestelltes Netzwerk aus
internen und externen Experten, die auf jeden Einzelfall
individuell eingehen können. Demographie-Managerin Dr.
Carolin Eitner ergänzt: „Mitarbeiter, Personalwesen,
Mitbestimmung und Führungskräfte suchen gemeinsam nach einer
guten Lösung, um den Erwerbsverlauf positiv zu gestalten. So
finden die Beschäftigten eine passende neue Aufgabe und das
Unternehmen bewahrt Fachwissen und Arbeitskraft.“
Kooperation statt Konkurrenz:
Betriebsübergreifendes Netzwerk schafft neue Möglichkeiten
Gerade in kleinen und
mittelständischen Unternehmen mit einer begrenzten Anzahl von
Arbeitsplätzen kann es aber allein aufgrund der Größe
schwierig werden, die eigenen Mitarbeiter intern an einem
anderen Platz einzusetzen. An dieser Stelle setzt TErrA an:
Gefördert durch das Bundesministerium für Bildung und
Forschung, hatten Experten aus Wissenschaft, Politik und
Wirtschaft unter Leitung des Bundesverbandes Deutscher
Berufsförderungswerke drei Jahre lang zusammengearbeitet und
erprobten die Idee eines überbetrieblichen Wechsels im
Zusammenspiel von Unternehmen unterschiedlicher Größe.
Als Praxispartner teilten
thyssenkrupp Steel und Entsorgung Dortmund EDG GmbH dabei ihr
Praxiswissen. Kern von TErrA ist ein umfassender
Beratungsprozess für Unternehmen und Beschäftigte mit Fokus
auf Tätigkeiten mit begrenzter Tätigkeitsdauer. Ein
präventiver Tätigkeitswechsel über eigene Unternehmensgrenzen
hinweg würde dabei vor allem für kleine und mittelständische
Betriebe enorme Chancen bergen, so das einhellige Resümee.
Catharina Schlaffke, Leiterin Inklusion und berufliche
Rehabilitation bei thyssenkrupp Steel: „Intern sind wir
bereits sehr gut aufgestellt. Aber der Austausch im Netzwerk
ist ein spannender Ansatz, der es wert ist, weiterverfolgt zu
werden: TErrA denkt in eine völlig neue Richtung mit enormen
sozialen und strukturellen Innovationen. In dieser Idee
steckt immenses Potenzial für die Zukunft, insbesondere für
KMUs.“
Das Zukunftsweisende an TErrA: „Der
Fokus auf den präventiven Erwerbsverlauf ist ein
zukunftsweisender Ansatz. Keiner bleibt auf der Strecke –
weder die Beschäftigten, die ihre Arbeit nicht mehr ausüben
können, noch die Unternehmen und Betriebe, die Know-how und
Leistungskraft erhalten“, sind sich Catharina Schlaffke und
Veit Echterhoff einig. Und so, das war das Credo der
Abschlussveranstaltung in Dortmund, sollte an den
Rahmenbedingungen gearbeitet werden, um die Voraussetzungen
für einen überbetrieblichen Wechsel zu schaffen. Ein Fazit,
das man zur im März anstehenden Abschlussveranstaltung nach
Berlin mitnehmen will.
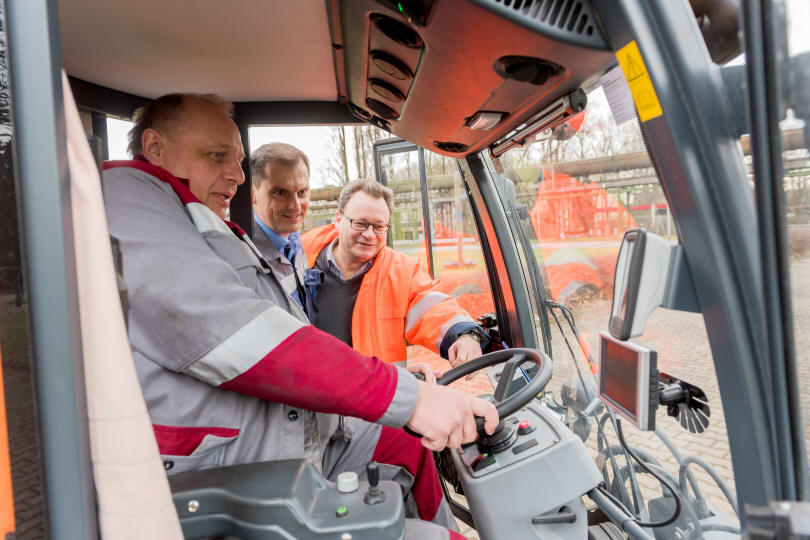
Leistungswandlung heißt nicht zwingend Leistungsausfall:
Im Rahmen des TErrA-Forschungsprojektes suchen Mitarbeiter,
Personalwesen und Führungskräfte gemeinsam nach Alternativen,
wenn der ursprüngliche Beruf nicht mehr ausgeübt werden kann.
Eine berufliche Weiterentwicklung und Einbindung in eine
passende neue Tätigkeit kann eine mögliche Lösung sein.
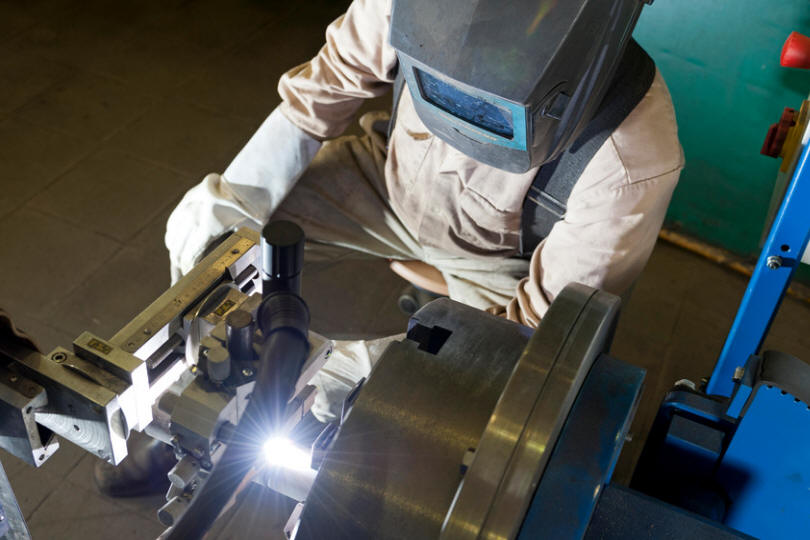
Kleine und mittelständische Unternehmen haben es aufgrund der
begrenzten Anzahl von Arbeitsplätzen schwer, die eigenen
Mitarbeiterinnen und Mitarbeiter an anderer Stelle
einzusetzen. In dem Netzwerk an Unternehmen, das durch TErrA
entstanden ist, besteht deshalb die Möglichkeit eines
überbetrieblichen Wechsels, zum Beispiel in den Stahlbereich
von thyssenkrupp.
|
|
Thyssenkrupp gibt Führungsstrukturen für künftige
Unternehmen bekannt
|
Essen/Duisburg, 12. Februar 2019 - Der Konzern
Thyssenkrupp hat heute die geplanten Führungsstrukturen der
beiden künftigen Unternehmen bekanntgegeben. Zum Start des
nächsten Geschäftsjahres am 1. Oktober sollen Thyssenkrupp
Industrials und Thyssenkrupp Materials ihre operative Arbeit
aufnehmen. In beiden zukünftigen Unternehmen werden die
Vorstandressorts auf jeweils drei reduziert.
Über die Besetzung wird im Frühjahr entschieden. Auch die
Konzern- und Servicefunktionen werden verringert. Im
Geschäftsjahr 2020/21 sollen die Verwaltungskosten für beide
Unternehmen insgesamt bei unter 300 Millionen Euro liegen
(2017/18: 380 Millionen Euro). Das Unternehmen schließt
betriebsbedingte Kündigungen aus. Die Hauptversammlung soll
im Januar 2020 final über die Pläne abstimmen.
In den ersten drei Monaten des laufenden Geschäftsjahres
verzeichnete Thyssenkrupp ein Umsatzplus von drei Prozent
auf 7,9 Milliarden Euro. Das operative Ergebnis EBIT betrug
168 Millionen Euro und blieb damit unter dem hohen Wert des
Vorjahresquartals. Infos:
www.thyssenkrupp.com
i
RWI: Deutsche Stahlerzeugung weiter rückläufig
Das RWI - Leibniz-Institut für Wirtschaftsforschung in Essen
erwartet, dass die Inlandsnachfrage nach Stahl in diesem
Jahr um 1,8 Prozent zurückgehen wird. Entsprechend sinke
auch die Roh- und Walzstahlerzeugung im zweiten Jahr in
Folge. Die Kapazitätsauslastung der deutschen Stahlwerke
nimmt voraussichtlich weiter leicht ab, bleibt aber mit gut
84 Prozent im internationalen Vergleich hoch. Während die
Beschäftigung in der deutschen Stahlindustrie im vergangenen
Jahr trotz ungünstiger Rahmenbedingungen zunahm, wird für
2019 ein Rückgang um 1,8 Prozent prognostiziert.
idr
|
|
|
|
|